Air dispersion of mineral fibers in ceiling tile manufacture
A technology of mineral fiber and suspended ceiling, which is applied in the direction of manufacturing tools, glass manufacturing equipment, fiber raw material processing, etc., and can solve the problems of reducing the strength of tiles
- Summary
- Abstract
- Description
- Claims
- Application Information
AI Technical Summary
Problems solved by technology
Method used
Image
Examples
Embodiment Construction
[0009] Traditionally, in the manufacture of wet felt acoustic tiles based on mineral wool, dilute aqueous slurries of mineral fibers and binders of starch and / or latex, and other small amounts of solid ingredients are used. The slurry is dispensed from the mixing tank onto a moving metal grid sometimes referred to simply as the wire. A mixing tank for the slurry is shown at 10 in FIG. 1 . It is common practice to receive bales 11 of mineral wool passed through belts or otherwise held in compression from a manufacturer or other source. As an example, the bale 11 may have a weight of 1000-1300 pounds and the mineral wool in the bale may be compressed to a density of, for example, between about 60 to about 65 pounds per cubic foot. When the restraint straps are released, the bag 11 will expand slightly on its own. The loose bales 11 are conveyed to a breaking bale station 12 where spiked rollers grab and separate the clumps 13 of mineral wool from the loose bales 11 . The aggl...
PUM
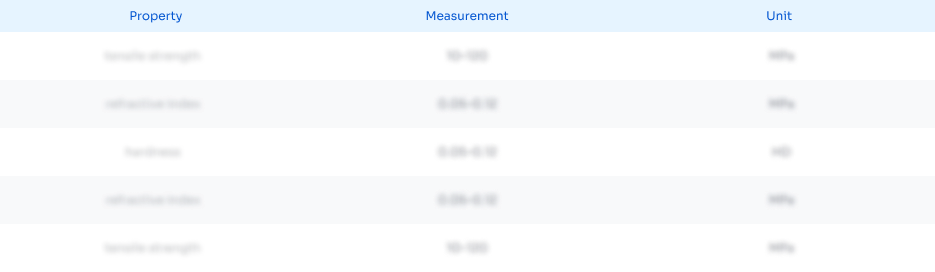
Abstract
Description
Claims
Application Information

- R&D Engineer
- R&D Manager
- IP Professional
- Industry Leading Data Capabilities
- Powerful AI technology
- Patent DNA Extraction
Browse by: Latest US Patents, China's latest patents, Technical Efficacy Thesaurus, Application Domain, Technology Topic, Popular Technical Reports.
© 2024 PatSnap. All rights reserved.Legal|Privacy policy|Modern Slavery Act Transparency Statement|Sitemap|About US| Contact US: help@patsnap.com