Mechanical arm
A technology of mechanical arms and mechanical grippers, applied in the field of mechanical arms, can solve the problems of inability to meet precision requirements, position control and easy to get stuck, and reduce detection efficiency, so as to achieve the effects of convenient control, precise positioning, and improved detection efficiency
- Summary
- Abstract
- Description
- Claims
- Application Information
AI Technical Summary
Problems solved by technology
Method used
Image
Examples
Embodiment
[0036] like Figure 1 to Figure 6 As shown, the mechanical arm includes X-axis guide rail assembly 1, Y-axis guide rail assembly 2, Z-axis guide rail assembly 3, X-axis motor 4, Y-axis motor 5, Z-axis motor 6, mechanical gripper 7 and mechanical gripper motor 8, The X-axis rail assembly 1 is connected to the X-axis motor 4, the Y-axis rail assembly 2 is connected to the Y-axis motor 5, the Z-axis rail assembly 3 is connected to the Z-axis motor 6, and the mechanical grip The hand 7 is connected to the mechanical gripper motor 8; the Y-axis guide rail assembly 2 is arranged on the X-axis guide rail assembly 1, the Z-axis guide rail assembly 3 is arranged on the Y-axis guide rail assembly 2, and the mechanical gripper 7 is arranged on the Z-axis guide rail assembly 3; the mechanical gripper 7 includes a gripper 7-6 and a detection device, and the detection device is arranged above the gripper 7-6.
[0037] The detection device includes a fixed block 7-1, an optocoupler 7-2, a s...
PUM
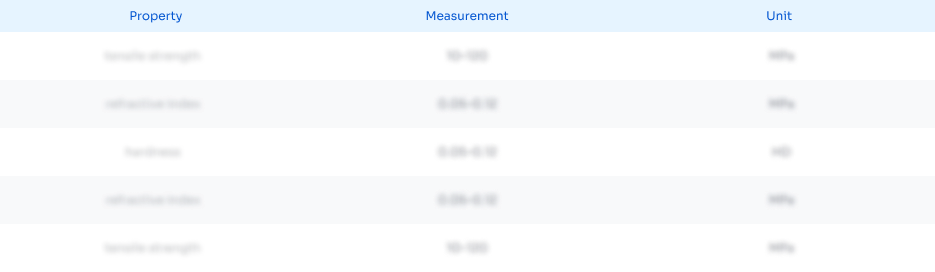
Abstract
Description
Claims
Application Information

- R&D
- Intellectual Property
- Life Sciences
- Materials
- Tech Scout
- Unparalleled Data Quality
- Higher Quality Content
- 60% Fewer Hallucinations
Browse by: Latest US Patents, China's latest patents, Technical Efficacy Thesaurus, Application Domain, Technology Topic, Popular Technical Reports.
© 2025 PatSnap. All rights reserved.Legal|Privacy policy|Modern Slavery Act Transparency Statement|Sitemap|About US| Contact US: help@patsnap.com