Dual-mass-block high sensitivity silicon micro resonant accelerometer structure based on two-level micro-levers
A technology of silicon micro-resonance and double-mass, which is applied in the direction of measurement of acceleration, velocity/acceleration/shock measurement, microstructure technology, etc., can solve the problem of low sensitivity of micro-mechanical accelerometers, large influence of environmental vibration and temperature, and complex structure and other problems to achieve the effect of eliminating vibration coupling, eliminating common mode interference, and improving sensitivity
- Summary
- Abstract
- Description
- Claims
- Application Information
AI Technical Summary
Problems solved by technology
Method used
Image
Examples
Embodiment Construction
[0017] The present invention will be further described below with reference to the accompanying drawings and specific embodiments.
[0018] like figure 1 As shown, the present invention is a dual-mass high-sensitivity silicon micro-resonance accelerometer structure based on a two-stage micro-lever, which is made by the bulk silicon process of single-crystal silicon, and the accelerometer structure includes a first mass 1 , the second mass 13, the first tuning fork resonator 2, the second tuning fork resonator 14, the first two-stage micro-lever amplification mechanism 4, the second-stage micro-lever amplification mechanism 5, and the third-stage micro-lever amplification mechanism 16 , the fourth-level micro-lever amplification mechanism 17, the first mass support beam 6, the second mass support beam 7, the third mass support beam 18, the fourth mass support beam 19, the first anchor point 3, the third mass support beam Second anchor point 8, third anchor point 9, fourth anch...
PUM
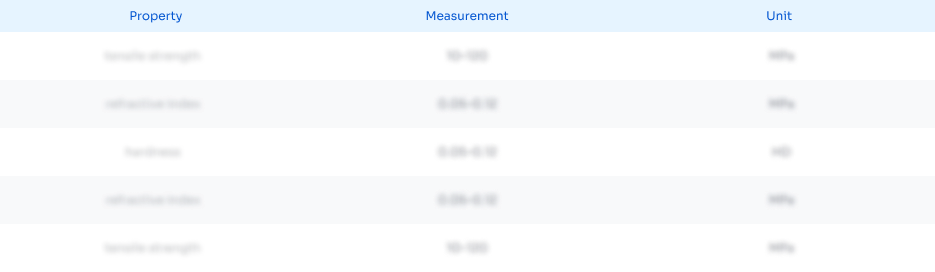
Abstract
Description
Claims
Application Information

- R&D Engineer
- R&D Manager
- IP Professional
- Industry Leading Data Capabilities
- Powerful AI technology
- Patent DNA Extraction
Browse by: Latest US Patents, China's latest patents, Technical Efficacy Thesaurus, Application Domain, Technology Topic, Popular Technical Reports.
© 2024 PatSnap. All rights reserved.Legal|Privacy policy|Modern Slavery Act Transparency Statement|Sitemap|About US| Contact US: help@patsnap.com