A battery-powered strain multi-dimensional force sensor fault diagnosis system
A multi-dimensional force sensor and fault diagnosis system technology, applied in the direction of measuring electrical variables, electronic circuit testing, instruments, etc., to achieve the effect of low power consumption and portability
- Summary
- Abstract
- Description
- Claims
- Application Information
AI Technical Summary
Problems solved by technology
Method used
Image
Examples
Embodiment Construction
[0018] The present invention will be further described below in conjunction with accompanying drawing and accompanying table.
[0019]The design idea of the present invention is: the short circuit of each bridge arm of strain gauge multi-dimensional force sensor measuring circuit, lead wire, open circuit fault all can cause the variation of resistance value between its output lead wire or between output lead wire and sensor substrate (structural steel body), therefore, Constant current can be directly fed into the output leads of the sensor measurement circuit, and the load resistance value can be calculated by detecting the voltage signal output by the constant current to diagnose short circuit and open circuit faults. For sensors with different resistance values of strain gauges, the present invention uses a digital-to-analog converter (DAC) combined with a voltage-current conversion (V / I) circuit to build a constant current excitation circuit, and the control core contro...
PUM
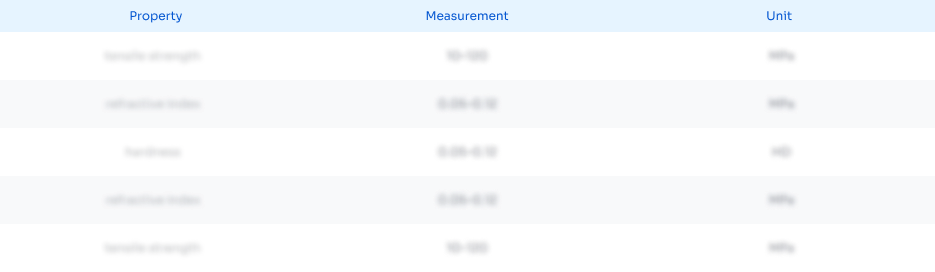
Abstract
Description
Claims
Application Information

- R&D Engineer
- R&D Manager
- IP Professional
- Industry Leading Data Capabilities
- Powerful AI technology
- Patent DNA Extraction
Browse by: Latest US Patents, China's latest patents, Technical Efficacy Thesaurus, Application Domain, Technology Topic, Popular Technical Reports.
© 2024 PatSnap. All rights reserved.Legal|Privacy policy|Modern Slavery Act Transparency Statement|Sitemap|About US| Contact US: help@patsnap.com