Guideway joint feature-considered vibration response analysis method for upright post-spindle system
A vibration response and joint technology, applied in the field of precision design of machine tool guide rail joints, can solve problems such as affecting calculation efficiency, non-convergence of equation solutions, and ignoring the dynamic characteristics of guide rail joints.
- Summary
- Abstract
- Description
- Claims
- Application Information
AI Technical Summary
Problems solved by technology
Method used
Image
Examples
Embodiment Construction
[0052] A method for analyzing the vibration response of a column-spindle system considering the characteristics of the joint of the guide rail. The specific implementation method is as follows: Step 1: Calculation of the equivalent stiffness of the rolling linear guide rail.
[0053] The above silver guide rail RGH45CA type roller linear guide is the research object, in which the material of the roller and groove (slider, guide rail) is roller bearing steel, and its specific parameters are:
[0054] Table 1 RGH45CA guide rail parameters
[0055]
[0056] Among them, the displacement and deformation conditions of the following rollers on the roller linear guide are:
[0057] δ 1 j δ 2 j ...
PUM
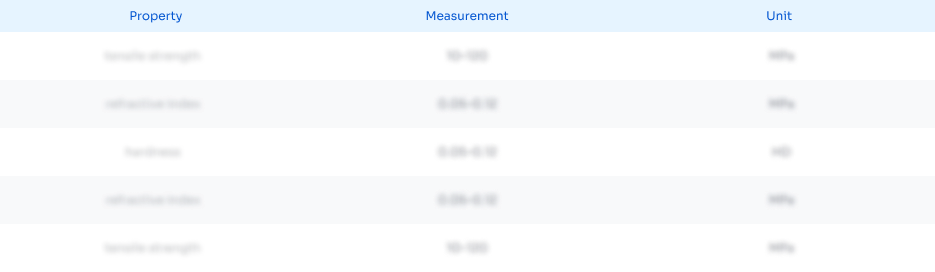
Abstract
Description
Claims
Application Information

- R&D
- Intellectual Property
- Life Sciences
- Materials
- Tech Scout
- Unparalleled Data Quality
- Higher Quality Content
- 60% Fewer Hallucinations
Browse by: Latest US Patents, China's latest patents, Technical Efficacy Thesaurus, Application Domain, Technology Topic, Popular Technical Reports.
© 2025 PatSnap. All rights reserved.Legal|Privacy policy|Modern Slavery Act Transparency Statement|Sitemap|About US| Contact US: help@patsnap.com