LED bulb lamp welding system
A technology of LED bulb lamps and welding systems, applied in welding equipment, auxiliary devices, metal processing, etc., can solve the problems of increased production costs, difficult management, high labor intensity, and low production efficiency
- Summary
- Abstract
- Description
- Claims
- Application Information
AI Technical Summary
Problems solved by technology
Method used
Image
Examples
Embodiment Construction
[0025] The present invention will be further described below in conjunction with the accompanying drawings and specific embodiments.
[0026] Such as Figure 1 to Figure 2 As shown, the LED bulb lamp welding system includes a frame 10. A turntable mechanism 2 is arranged on the frame 10. The turntable mechanism 2 includes a disc 21 and a turntable motor that drives the disc 21 to rotate. The disc 21 is arranged along the circumferential direction. There are multiple material levels, and each material level is respectively equipped with a rotating chuck mechanism 22 for fixing the bulb lamp. The outer side of the disc 21 is sequentially equipped with a side welding mechanism 4, a top welding mechanism 5, a rosin removal mechanism 1, and a feeding mechanism 6. The turntable motor drives the disc 21 to rotate, and the rotating chuck mechanism 22 is used to clamp the LED bulb lamp to be welded. The side welding mechanism 4 welds the sides of the LED bulb lamp, and the top welding ...
PUM
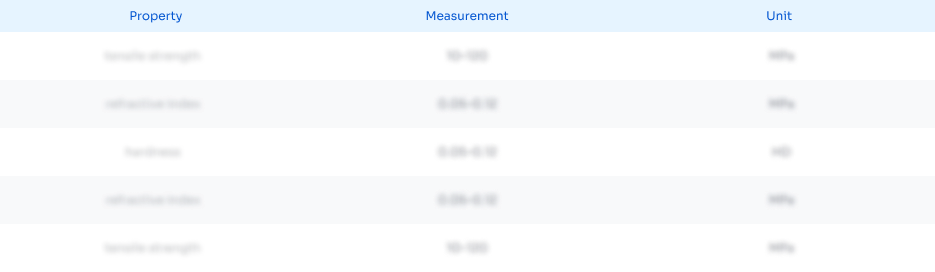
Abstract
Description
Claims
Application Information

- R&D
- Intellectual Property
- Life Sciences
- Materials
- Tech Scout
- Unparalleled Data Quality
- Higher Quality Content
- 60% Fewer Hallucinations
Browse by: Latest US Patents, China's latest patents, Technical Efficacy Thesaurus, Application Domain, Technology Topic, Popular Technical Reports.
© 2025 PatSnap. All rights reserved.Legal|Privacy policy|Modern Slavery Act Transparency Statement|Sitemap|About US| Contact US: help@patsnap.com