Automatic welding system for crane bogie frames
An automatic welding and trolley frame technology, applied in welding equipment, auxiliary welding equipment, welding/cutting auxiliary equipment, etc., can solve the problems of increased labor intensity, unstable product quality, low production efficiency, etc., and shorten the turning time , good system flexibility, and the effect of improving production efficiency
- Summary
- Abstract
- Description
- Claims
- Application Information
AI Technical Summary
Problems solved by technology
Method used
Image
Examples
Embodiment 1
[0019] Such as figure 1 , figure 2 , image 3 , Figure 4 and Figure 5 As shown, an automatic welding system for a crane frame, which includes a flexible tooling fixture and a robot welding system, the flexible tooling fixture includes a base 1, and the upper end of the base 1 is respectively provided with a bottom pressing block A2 and a bottom Pressing block B15, the middle part of the right side of the base 1 is provided with a column A4, the middle part of the column A4 is provided with a compression bolt A3, and the center of the top of the column A4 is provided with a hydraulic rod A5. The top of the hydraulic rod A5 is provided with a connecting block A7, the connecting block A7 is provided with a fixed block A6, the left side of the fixed block A6 is provided with an upper pressure block A8, and the left middle of the base 1 is provided There is a column B10, the middle part of the column B10 is provided with a compression bolt B9, the center of the top of the co...
Embodiment 2
[0022] Such as figure 1 , figure 2 , image 3 , Figure 4 and Figure 5 As shown, an automatic welding system for a crane frame, which includes a flexible tooling fixture and a robot welding system, the flexible tooling fixture includes a base 1, and the upper end of the base 1 is respectively provided with a briquetting block A2 and a briquetting block B14, the middle part of the right side of the base 1 is provided with a column A4, the middle part of the column A4 is provided with a compression bolt A3, and the center of the top of the column A4 is provided with a positioning rod A5, and the positioning rod The top of A5 is provided with a positioning block A6, the top of the positioning block A6 is provided with a pin A12, the middle part of the left side of the base 1 is provided with a column B8, and the middle part of the column B8 is provided with a compression bolt B7 , the center of the top of the column B8 is provided with a positioning rod B9, the top of the p...
PUM
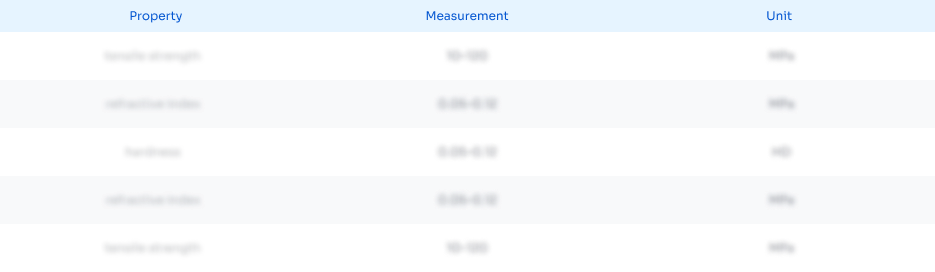
Abstract
Description
Claims
Application Information

- R&D
- Intellectual Property
- Life Sciences
- Materials
- Tech Scout
- Unparalleled Data Quality
- Higher Quality Content
- 60% Fewer Hallucinations
Browse by: Latest US Patents, China's latest patents, Technical Efficacy Thesaurus, Application Domain, Technology Topic, Popular Technical Reports.
© 2025 PatSnap. All rights reserved.Legal|Privacy policy|Modern Slavery Act Transparency Statement|Sitemap|About US| Contact US: help@patsnap.com