Distributed multi-rotor-wing unmanned aerial vehicle system with heavy load and long endurance
A multi-rotor UAV, distributed technology, applied in the direction of rotorcraft, unmanned aircraft, motor vehicles, etc., can solve the restrictions on the application and development of multi-rotor UAVs, inconvenient maintenance, transportation and mass production, flight Problems such as limited time and load capacity, etc., to achieve the effect of easy maintenance, space saving and weight reduction
- Summary
- Abstract
- Description
- Claims
- Application Information
AI Technical Summary
Problems solved by technology
Method used
Image
Examples
Embodiment Construction
[0023] Such as Figure 1 to Figure 9 As shown, a distributed heavy-duty long-endurance multi-rotor UAV system includes an independent fuselage 1 and a distributed fuselage 2. The independent fuselage 1 includes a standard box 101 and a box arm 102. Each standard box 101 is equipped with at least 3 box arms, and the box arm 102 adopts an upper and lower double box arm structure, and the distributed body 2 is fixed on the box arm 102 of the independent body 1; the distributed body 2 includes Power system 201, machine arm 202 and electronic system 203, described power system 201 is installed on the upper end of machine arm 202, and electronic system 203 is installed on the lower end of machine arm 202; Described power system 201 comprises rotor 2011, engine 2012, oil pump 2013 , the fuel tank 2014 and the steering gear 2015, the rotor 2011 is connected to the engine 2015 and located above the steering gear 2015, the oil pump 2013 is connected to the fuel tank 2014 and located bel...
PUM
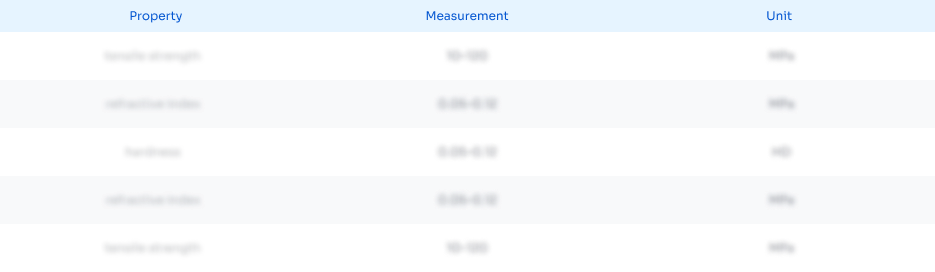
Abstract
Description
Claims
Application Information

- Generate Ideas
- Intellectual Property
- Life Sciences
- Materials
- Tech Scout
- Unparalleled Data Quality
- Higher Quality Content
- 60% Fewer Hallucinations
Browse by: Latest US Patents, China's latest patents, Technical Efficacy Thesaurus, Application Domain, Technology Topic, Popular Technical Reports.
© 2025 PatSnap. All rights reserved.Legal|Privacy policy|Modern Slavery Act Transparency Statement|Sitemap|About US| Contact US: help@patsnap.com