Machining process method for plywood
A processing technology, plywood technology, applied in the field of wood processing, can solve the problems of high price, poor quality, loss and waste, etc.
- Summary
- Abstract
- Description
- Claims
- Application Information
AI Technical Summary
Problems solved by technology
Method used
Examples
Embodiment 1
[0018] This embodiment provides a kind of processing method of plywood, and the operation steps are as follows:
[0019] 1) Log processing: Saw the logs, then cook and peel them, and peel the peeled wood sections for veneer peeling.
[0020] 2) Drying: The veneer after rotary cutting is firstly cleaned, and then dried at a temperature of 73° C., and finally cooled at room temperature.
[0021] 3) Gluing treatment: apply a layer of adhesive to the surface of the veneer after rotary cutting, stack 6-8 veneers together, and add a piece of camphor veneer on both sides of the superimposed veneer.
[0022] 4) Press plate molding: Fix the veneer in step 3) on the die sleeve of the press machine, control the temperature at 81°C, and press the plate for 3 hours.
[0023] The log used in the log processing step is poplar.
[0024] The drying time in the drying operation step is 2 hours.
[0025] The plywood after the press plate molding is carried out vacuum drying again, and the dry...
Embodiment 2
[0027] This embodiment provides a kind of processing method of plywood, and the operation steps are as follows:
[0028] 1) Log processing: Saw the logs, then cook and peel them, and peel the peeled wood sections for veneer peeling.
[0029] 2) Drying: The veneer after rotary cutting is firstly cleaned, and then dried at a temperature of 61° C., and finally cooled at room temperature.
[0030] 3) Gluing treatment: apply a layer of adhesive to the surface of the veneer after rotary cutting, stack 6-8 veneers together, and add a piece of camphor veneer on both sides of the superimposed veneer.
[0031] 4) Press plate molding: Fix the veneer in step 3) on the mold sleeve of the press machine, control the temperature at 93°C, and press the plate for 2.5 hours.
[0032] The log used in the log processing step is poplar.
[0033] The drying time in the drying operation step is 1 hour.
[0034] The plywood after the pressed plate is formed is vacuum-dried again, and the drying tem...
Embodiment 3
[0036] This embodiment provides a kind of processing method of plywood, and the operation steps are as follows:
[0037] 1) Log processing: Saw the logs, then cook and peel them, and peel the peeled wood sections for veneer peeling.
[0038] 2) Drying: The veneer after rotary cutting is firstly cleaned, and then dried at a temperature of 67° C., and finally cooled at room temperature.
[0039] 3) Gluing treatment: apply a layer of adhesive to the surface of the veneer after rotary cutting, stack 6-8 veneers together, and add a piece of camphor veneer on both sides of the superimposed veneer.
[0040] 4) Press plate molding: Fix the veneer in step 3) on the die sleeve of the press machine, control the temperature at 86°C, and press the plate for 2.6 hours.
[0041] The drying time in the drying operation step was 1.7 hours.
[0042] The plywood after pressing is then vacuum-dried. The drying temperature is controlled at 24° C. for 4.5 hours.
PUM
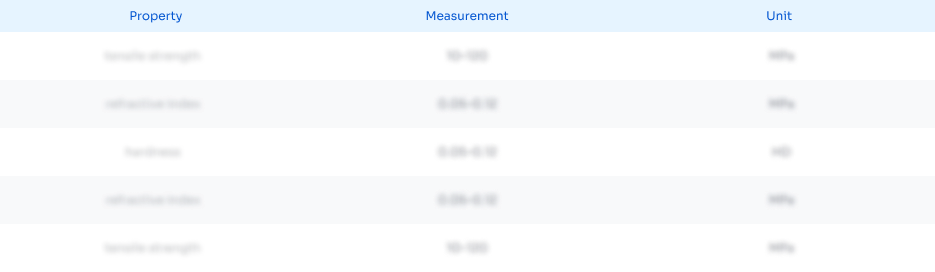
Abstract
Description
Claims
Application Information

- Generate Ideas
- Intellectual Property
- Life Sciences
- Materials
- Tech Scout
- Unparalleled Data Quality
- Higher Quality Content
- 60% Fewer Hallucinations
Browse by: Latest US Patents, China's latest patents, Technical Efficacy Thesaurus, Application Domain, Technology Topic, Popular Technical Reports.
© 2025 PatSnap. All rights reserved.Legal|Privacy policy|Modern Slavery Act Transparency Statement|Sitemap|About US| Contact US: help@patsnap.com