A multi-degree-of-freedom manipulator based on sequential control
A technology with timing control and degrees of freedom, applied in the field of manipulators, can solve the problems of inaccurate positioning of mechanical fingers, virtual swing of fingers, and high technical maturity requirements, and achieve the effect of simplified structure and strong practicability.
- Summary
- Abstract
- Description
- Claims
- Application Information
AI Technical Summary
Problems solved by technology
Method used
Image
Examples
Embodiment Construction
[0047] Such as Figure 19 As shown, it includes mechanical third subfinger, mechanical second subfinger, mechanical first subfinger, palm plate, mechanical main finger, motor drive mechanism fixing plate, motor drive mechanism, arm sleeve, main finger side swing steel wire, Main finger side swing wire guide hole support, main finger side swing spring, main finger side swing spring support, main finger swing block support, main finger swing block, main finger swing cylindrical pin, first and second finger side swing spring, first pair The finger swing block, the side swing steel wire of the first pair of fingers, and the guide hole support of the side swing steel wire of the first pair of fingers, among which the second mechanical finger and the third mechanical third finger are installed side by side on the side of the palm board in sequence, as shown in Figure 23 As shown, the swing block of the first secondary finger is installed on the first secondary finger of the machine...
PUM
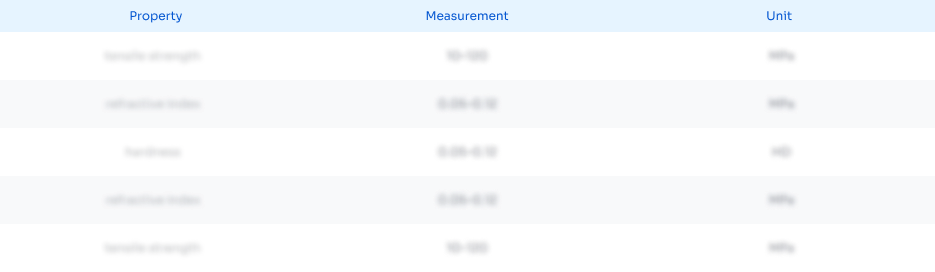
Abstract
Description
Claims
Application Information

- R&D
- Intellectual Property
- Life Sciences
- Materials
- Tech Scout
- Unparalleled Data Quality
- Higher Quality Content
- 60% Fewer Hallucinations
Browse by: Latest US Patents, China's latest patents, Technical Efficacy Thesaurus, Application Domain, Technology Topic, Popular Technical Reports.
© 2025 PatSnap. All rights reserved.Legal|Privacy policy|Modern Slavery Act Transparency Statement|Sitemap|About US| Contact US: help@patsnap.com