An ultra-deep mine hoist multi-rope cooperative control system test bench
A mine hoist and collaborative control technology, which is applied to mine hoisting equipment, elevators, transportation and packaging, etc., can solve problems such as complex working conditions, difficult on-site testing of hoisting equipment, and restrictions on the development and utilization of deep resources. Ease of maintenance and simple operation
- Summary
- Abstract
- Description
- Claims
- Application Information
AI Technical Summary
Problems solved by technology
Method used
Image
Examples
Embodiment 1
[0015] Example 1: figure 1 and figure 2 Among them, the control system test bench includes: four hydraulic motors 1 and corresponding four rollers 2 and four steel wire ropes 3, a set of steel structure supports 4, four hinges 5, four servo hydraulic cylinders 6, and four linear guide rails 7 , four sky wheels 8, four sky wheel brackets 9, four pressure sensors 10, four tension sensors 11, a gyroscope 12, a cage 13, four couplings 14, motor base 15, an oil pump 16 and controller;
[0016] The hydraulic motor 1 is connected to the drum 2 through a coupling 14. There is a steel wire rope 3 on the drum 2, and the steel wire rope 3 is connected to the cage 13; To the hinge 5, the upper end is connected with the sky wheel bracket 9, the sky wheel bracket 9 is connected with the sky wheel 8; the sky wheel bracket 9 is fixed on the linear guide rail 7, the hinge 5 and the linear guide rail 7 are connected on the steel structure bracket 4, and the servo The hydraulic cylinder 6 dr...
PUM
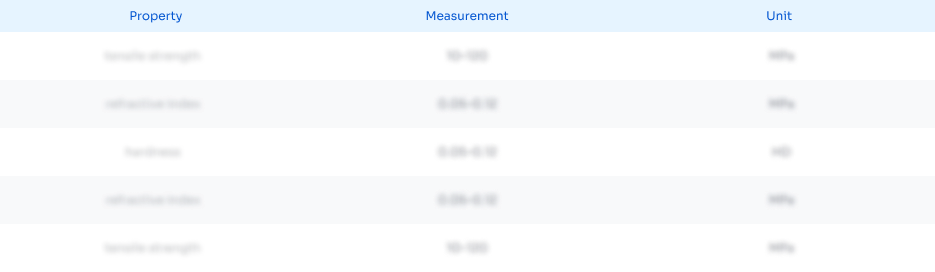
Abstract
Description
Claims
Application Information

- R&D
- Intellectual Property
- Life Sciences
- Materials
- Tech Scout
- Unparalleled Data Quality
- Higher Quality Content
- 60% Fewer Hallucinations
Browse by: Latest US Patents, China's latest patents, Technical Efficacy Thesaurus, Application Domain, Technology Topic, Popular Technical Reports.
© 2025 PatSnap. All rights reserved.Legal|Privacy policy|Modern Slavery Act Transparency Statement|Sitemap|About US| Contact US: help@patsnap.com