Low-sulfur discharging and sulfur recycling process of intermediate concentration acid gas
A sulfur recovery and acid gas technology, applied in chemical recovery, sulfur preparation/purification, energy input, etc., to achieve good safe operation conditions, simple scrapping procedures, and good scrapping treatment conditions
- Summary
- Abstract
- Description
- Claims
- Application Information
AI Technical Summary
Problems solved by technology
Method used
Image
Examples
Embodiment 1
[0040] A set of 10,000 tons / year sulfur recovery unit, including a direct oxidation reactor, a selective oxidation reactor and two adsorption desulfurization towers that can be connected in series and parallel; the direct oxidation reactor is filled with TiO 2 Sulfur recovery catalyst 60m 3 , the catalyst is loaded in 6 layers, with air inlets and cooling coils between the layers; the selective oxidation reactor is filled with Fe 2 o 3 / SiO 2 selective oxidation of H 2 S Catalyst 60m 3 , the catalyst is packed in 6 layers, with air inlets and cooling coils between the layers; the two adsorption desulfurization towers are filled with Na 2 CO 3 / Activated carbon catalytic oxidation adsorption desulfurizer 200m 3 ; The basic operating conditions of the device are:
[0041] 1) Acid gas 20000m 3 / hr,H 2 S volume content 5.0%, the rest is mainly CO 2 , COS≤20mg / m 3 , SO 2 ≤100mg / m 3 , without CS 2 , in the direct oxidation reactor and the air 2200m 3 Reaction around ...
Embodiment 2
[0052] A set of 10,000 tons / year sulfur recovery unit, including a direct oxidation reactor, a selective oxidation reactor and two adsorption desulfurization towers that can be connected in series and parallel; the direct oxidation reactor is filled with TiO 2 Sulfur Recovery Catalyst 40m 3 , the catalyst is loaded in 6 layers, with air inlets and cooling coils between the layers; the selective oxidation reactor is filled with Fe 2 o 3 / SiO 2 selective oxidation of H 2 S Catalyst 40m 3 , the catalyst is packed in 6 layers, with air inlets and cooling coils between the layers; the two adsorption desulfurization towers are filled with Fe 2 o 3 / Activated carbon catalytic oxidation adsorption desulfurizer 125m 3 ; The basic operating conditions of the device are:
[0053] 1) Acid gas 5000m 3 / hr,H 2 S volume content 20%, the rest is mainly CO 2 , SO 2 ≤100mg / m 3 , excluding COS, CS 2 , mercaptan, sulfide and other organic sulfur, in the direct oxidation reactor and ...
PUM
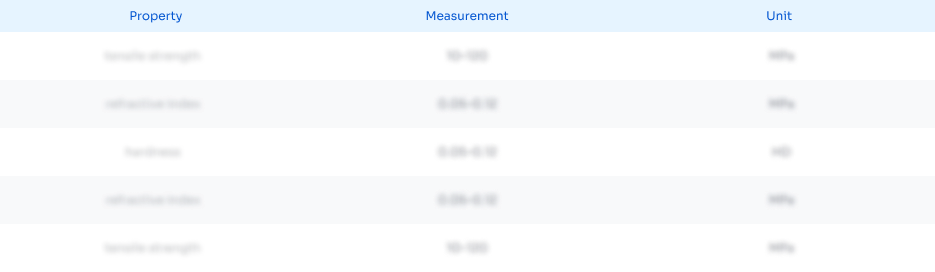
Abstract
Description
Claims
Application Information

- Generate Ideas
- Intellectual Property
- Life Sciences
- Materials
- Tech Scout
- Unparalleled Data Quality
- Higher Quality Content
- 60% Fewer Hallucinations
Browse by: Latest US Patents, China's latest patents, Technical Efficacy Thesaurus, Application Domain, Technology Topic, Popular Technical Reports.
© 2025 PatSnap. All rights reserved.Legal|Privacy policy|Modern Slavery Act Transparency Statement|Sitemap|About US| Contact US: help@patsnap.com