A method of bushing loading
A bushing and loading module technology, applied in measuring devices, instruments, etc., can solve the problems of large changes in shafting preload, unfavorable mass production, long assembly shafting cycle, etc., to improve assembly accuracy and ensure parallelism. Effect
- Summary
- Abstract
- Description
- Claims
- Application Information
AI Technical Summary
Problems solved by technology
Method used
Image
Examples
Embodiment Construction
[0020] A bushing loading method of the present invention will be described in detail below with reference to the drawings and specific embodiments.
[0021] Such as figure 1 and figure 2 As shown, the shafting of the dynamic tuning gyroscope includes an upper bearing 201, an outer ring bushing 202, and a lower bearing 203. For the assembly of the shafting of the dynamic tuning gyroscope, a bushing loading method of the present invention includes the following steps:
[0022] Step 1. Install the upper bearing 201 on the upper end of the drive shaft 204 in a back-to-back installation mode, and fix the inner ring of the upper bearing 201 on the drive shaft 204 by gluing or other methods. Epoxy glue can be used for the gluing. The stability of the fixation between the bearing 201 and the drive shaft 204 can be enhanced by curing epoxy glue;
[0023] Step 2: Turn the drive shaft 204 upside down, put the outer ring bush 202 on the drive shaft 204, keep the end face of the outer r...
PUM
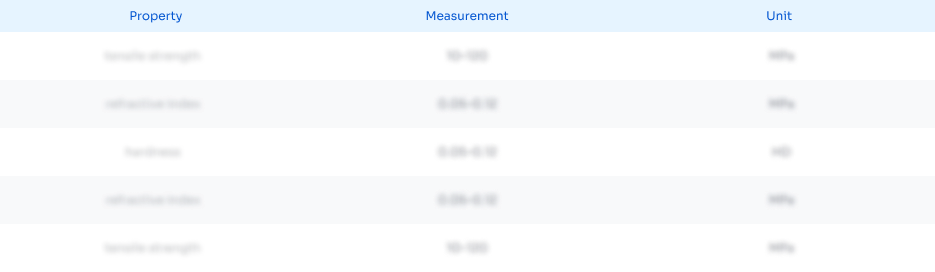
Abstract
Description
Claims
Application Information

- R&D
- Intellectual Property
- Life Sciences
- Materials
- Tech Scout
- Unparalleled Data Quality
- Higher Quality Content
- 60% Fewer Hallucinations
Browse by: Latest US Patents, China's latest patents, Technical Efficacy Thesaurus, Application Domain, Technology Topic, Popular Technical Reports.
© 2025 PatSnap. All rights reserved.Legal|Privacy policy|Modern Slavery Act Transparency Statement|Sitemap|About US| Contact US: help@patsnap.com