Vibration resistance installation method for temperature compensation crystal oscillator
An installation method and technology of temperature-compensated crystal oscillator, which are applied in the field of satellite navigation, can solve the problems of reducing satellite signal acquisition, tracking performance, deterioration of crystal oscillator phase noise indicators, etc., and achieve the effect of reducing overall vibration and improving acquisition.
- Summary
- Abstract
- Description
- Claims
- Application Information
AI Technical Summary
Problems solved by technology
Method used
Image
Examples
Embodiment 1
[0017] figure 1 Shown is the installation position of the crystal oscillator 2 on the circuit board 1. The crystal oscillator should be as far away from the center of the circuit board as possible with the largest vibration amplitude, and located at the corner of the circuit board 1 or near the mounting hole 3. The circuit board 1 passes through the mounting hole 3 and screws are fixed on the base.
Embodiment 2
[0019] On the basis of Embodiment 1, a reinforcement structure 4 is arranged around the crystal oscillator 2 to enhance the local rigidity of the circuit board, and the reinforcement structure 4 is as figure 2 As shown, it is in the shape of a quadrangular frame, and the crystal oscillator 2 is enclosed inside the quadrangular frame, and mounting holes 3 are provided on the four corners of the quadrangular frame, and one of the long sides of the quadrangular frame extends to the edge of the circuit board, where it extends An installation hole 3 is also provided at the end of the direction, and the reinforcement structure 4 is connected with the circuit board 1 as a whole through screws and the installation hole 3 .
Embodiment 3
[0021] On the basis of Embodiment 2, a shell structural member 5 is also provided outside the circuit board 1. The upper end of the shell structural member 5 is closed, the bottom surface is open, and the shape of the surrounding is consistent with the shape of the circuit board 1. Above the board 1, a boss is provided at the corresponding installation position of the reinforcement structure 4 on the inner side of the shell structure 5, which is used to reduce the vibration of the circuit board and facilitate installation. At the position where the boss corresponds to the mounting hole 3 on the reinforcement structure 4, a mounting hole 3 is also provided, and the circuit board 1, the reinforcement structure 4 and the shell structure 5 pass through the mounting hole 3 and through the mounting hole. 3 screws are fixedly connected as one, such as image 3 shown.
PUM
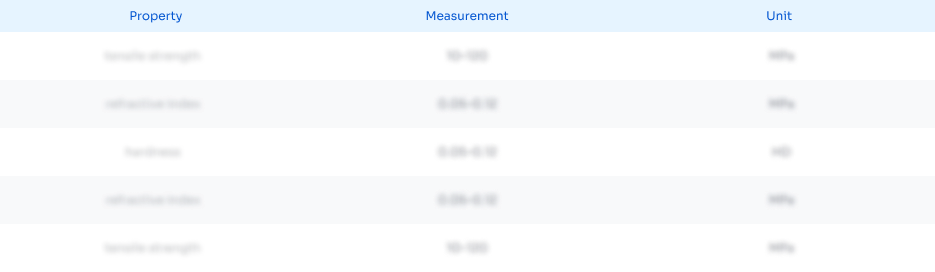
Abstract
Description
Claims
Application Information

- R&D
- Intellectual Property
- Life Sciences
- Materials
- Tech Scout
- Unparalleled Data Quality
- Higher Quality Content
- 60% Fewer Hallucinations
Browse by: Latest US Patents, China's latest patents, Technical Efficacy Thesaurus, Application Domain, Technology Topic, Popular Technical Reports.
© 2025 PatSnap. All rights reserved.Legal|Privacy policy|Modern Slavery Act Transparency Statement|Sitemap|About US| Contact US: help@patsnap.com