Rotor type double-stage oil pump
A technology of oil pump and rotor type, which is applied in the field of rotor type two-stage oil pump structure, and can solve the problem of high cost
- Summary
- Abstract
- Description
- Claims
- Application Information
AI Technical Summary
Problems solved by technology
Method used
Image
Examples
Embodiment Construction
[0009] Such as figure 1 , 2 A rotor-type two-stage oil pump is shown, which includes a main pump body 1, a main pump inner rotor 4, a main pump outer rotor 5, a driving shaft 6, an intermediate partition plate 2, an auxiliary pump body 3, and an inner Rotor 7, auxiliary pump outer rotor 8; the main pump body 1 is located above the auxiliary pump body 3, the middle partition 2 is located between the main pump body 1 and the auxiliary pump body 3, the The middle partition plate 2 is provided with a main pump oil inlet 9 and a main pump oil outlet 10, and the lower part of the auxiliary pump body 3 is provided with an auxiliary pump oil inlet 11 and an auxiliary pump oil outlet 12; the main pump The inner rotor 4 and the main pump outer rotor 5 are located in the rotor cavity of the main pump body 1, and the auxiliary pump inner rotor 7 and the auxiliary pump outer rotor 8 are located in the rotor cavity of the auxiliary pump body 3; the drive shaft 6 is simultaneously Through ...
PUM
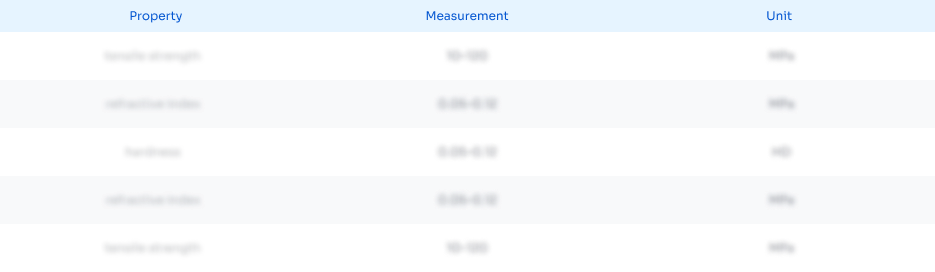
Abstract
Description
Claims
Application Information

- R&D Engineer
- R&D Manager
- IP Professional
- Industry Leading Data Capabilities
- Powerful AI technology
- Patent DNA Extraction
Browse by: Latest US Patents, China's latest patents, Technical Efficacy Thesaurus, Application Domain, Technology Topic, Popular Technical Reports.
© 2024 PatSnap. All rights reserved.Legal|Privacy policy|Modern Slavery Act Transparency Statement|Sitemap|About US| Contact US: help@patsnap.com