Mechanical arm system and its parallelism correction method
A technique for manipulators and calibration methods, which is applied to manipulators, program-controlled manipulators, instruments, etc., and can solve problems such as the inability to ensure the parallelism between the manipulator and the machine, the difficulty of parallelism correction, and the difficulty in parallelism correction.
- Summary
- Abstract
- Description
- Claims
- Application Information
AI Technical Summary
Problems solved by technology
Method used
Image
Examples
Embodiment Construction
[0020] The detailed structure, features, assembly or usage of the robotic arm system and its parallelism correction method provided by the present invention will be described in the subsequent detailed description of the implementation. However, those skilled in the field of the present invention should understand that these detailed descriptions and specific examples for implementing the present invention are only for illustrating the present invention, and are not intended to limit the scope of patent application of the present invention.
[0021] The applicant first explains here that in the embodiments and drawings to be described below, the same reference numerals denote the same or similar components or structural features. Secondly, when it is mentioned that a component is set on another component, it means that the aforementioned component is directly set on the other component, or that the aforementioned component is indirectly set on the other component, that is, ther...
PUM
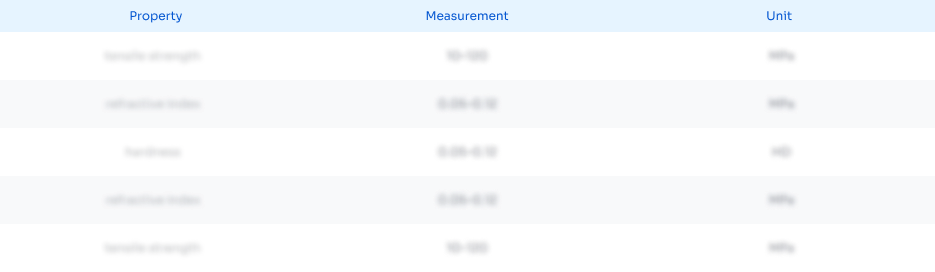
Abstract
Description
Claims
Application Information

- Generate Ideas
- Intellectual Property
- Life Sciences
- Materials
- Tech Scout
- Unparalleled Data Quality
- Higher Quality Content
- 60% Fewer Hallucinations
Browse by: Latest US Patents, China's latest patents, Technical Efficacy Thesaurus, Application Domain, Technology Topic, Popular Technical Reports.
© 2025 PatSnap. All rights reserved.Legal|Privacy policy|Modern Slavery Act Transparency Statement|Sitemap|About US| Contact US: help@patsnap.com