A high-frequency ultrasonic polishing device and method using a matching layer composite piezoelectric vibrator
A piezoelectric vibrator and matching layer technology, which is applied in the field of high-frequency ultrasonic composite polishing devices, can solve the problems of difficult frequency increase, limited ultrasonic energy, difficulty in efficient use of ultrasonic vibration and global flattening of workpieces, etc., to achieve flexible attachment and structure simple effect
- Summary
- Abstract
- Description
- Claims
- Application Information
AI Technical Summary
Problems solved by technology
Method used
Image
Examples
Embodiment Construction
[0015] The present invention will be described in further detail below in conjunction with the embodiments shown in the accompanying drawings.
[0016] The labels in the figure are: 1. Piezoelectric ceramics; 2. Matching layer I; 3. Matching layer II (part to be polished); 4. Brush slip ring; 5. Weight; 6. Polishing liquid; 7. Polishing pad; 8. Polishing workbench;
[0017] The shaft hole of the brush slip ring 4 is connected with the weight 5 through clearance fit, and the leading wire of the slip ring 4 is connected to the piezoelectric ceramic sheet 1 through the middle through hole of the weight 5, and the piezoelectric ceramic sheet 1 is made of epoxy resin The adhesive is pasted on the matching layer I, the matching layer II is adsorbed on the matching layer I by the water of the polishing piece, and the polishing pad 7 is pasted on the polishing workbench 8 .
[0018] The traditional low-frequency power ultrasonic vibrator has a complex structure, and is limited by the...
PUM
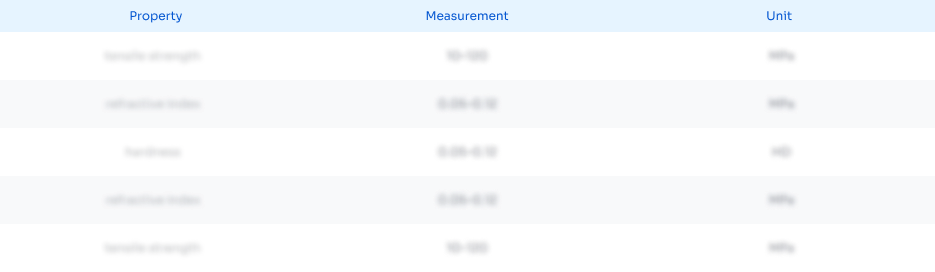
Abstract
Description
Claims
Application Information

- R&D Engineer
- R&D Manager
- IP Professional
- Industry Leading Data Capabilities
- Powerful AI technology
- Patent DNA Extraction
Browse by: Latest US Patents, China's latest patents, Technical Efficacy Thesaurus, Application Domain, Technology Topic, Popular Technical Reports.
© 2024 PatSnap. All rights reserved.Legal|Privacy policy|Modern Slavery Act Transparency Statement|Sitemap|About US| Contact US: help@patsnap.com