Reverse Extrusion Active Floating Die Forming System and Forming Process
A forming process and active technology, which is applied in the field of forging and forging in material processing engineering, can solve the problems of large temperature drop and poor forming force reduction effect, and achieve the purpose of reducing temperature drop, reducing changes in physical properties, and preventing strength reduction. Effect
- Summary
- Abstract
- Description
- Claims
- Application Information
AI Technical Summary
Problems solved by technology
Method used
Image
Examples
Embodiment 1
[0032] The first embodiment is basically as attached figure 1 Shown: a back-extrusion active floating die forming system, including an upper template 1 and a lower die pad 10. The lower die pad 10 is fixedly connected to the quick forging hydraulic press, the upper template 1 is set above the lower die pad 10, and the upper template 1. The upper mold fixing block 2 is welded underneath, the right side of the upper mold fixing block 2 is threadedly connected with a contact rod 7, an electromagnetic switch is provided under the contact rod 7, and a punch 4 is connected to the upper mold fixing block 2. The upper die gasket 3 is provided between the upper die fixing block 2 and the punch 4, the lower die gasket 10 is threadedly connected with an annular hydraulic cylinder 6, and the annular hydraulic cylinder 6 is fixedly connected with a concave mold 5, which is provided with Through the cavity of the die 5, the punch 4 is in clearance fit with the cavity. The cavity is slidably ...
Embodiment 2
[0040] The second embodiment: the difference from the first embodiment is that the moving speed of the die 5 is 5 times the upward moving speed of the blank 8;
[0041] The back-extrusion active floating die forming process includes the following steps:
[0042] (1) First use a heating tube to preheat the mold to 350°C;
[0043] (2) The blank 8 is continuously heated by an external induction heater to 1250℃;
[0044] (3) Set the speed of punch 4 to 40mm / s, the movement speed of annular hydraulic cylinder 6 to 200mm / s, and the speed ratio of punch 4 to die 5 to 1:5;
[0045] (5) After driving the upper mold plate 1 to move downwards, the upper mold plate 1 drives the upper mold fixing block 2 to move downwards, and the upper mold fixing block 2 drives the upper mold gasket 3 and the punch 4 to move downwards into the cavity. When the lower end of the punch 4 touches the blank 8 and presses it down by 10mm, the die core 9 supports the blank 8 and abuts against the blank 8, the contact ro...
Embodiment 3
[0046] The third embodiment: the difference from the first embodiment is that the moving speed of the die 5 is 0.5 times the upward moving speed of the blank 8;
[0047] The back-extrusion active floating die forming process includes the following steps:
[0048] (1) First use a heating tube to preheat the mold to 300°C;
[0049] (2) The blank 8 is continuously heated by an external induction heater to 1200°C;
[0050] (3) Set the speed of the punch 4 to 200mm / s, the movement speed of the annular hydraulic cylinder 6 to 100mm / s, and the speed ratio of the punch 4 to the die 5 to be 1:0.5;
[0051] (5) After driving the upper mold plate 1 to move downwards, the upper mold plate 1 drives the upper mold fixing block 2 to move downwards, and the upper mold fixing block 2 drives the upper mold gasket 3 and the punch 4 to move downwards into the cavity. When the lower end of the punch 4 touches the blank 8 and presses it down by 5mm, the die core 9 supports the blank 8 and abuts against the ...
PUM
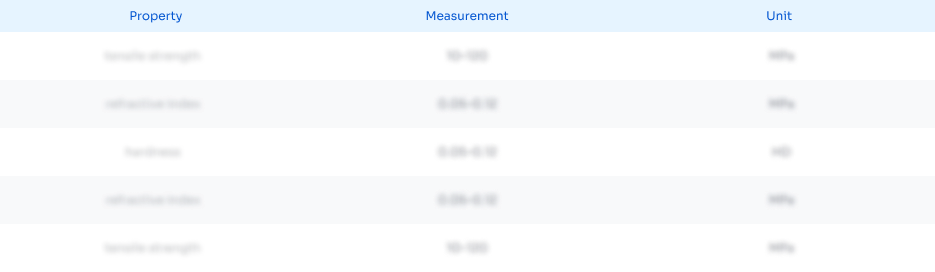
Abstract
Description
Claims
Application Information

- Generate Ideas
- Intellectual Property
- Life Sciences
- Materials
- Tech Scout
- Unparalleled Data Quality
- Higher Quality Content
- 60% Fewer Hallucinations
Browse by: Latest US Patents, China's latest patents, Technical Efficacy Thesaurus, Application Domain, Technology Topic, Popular Technical Reports.
© 2025 PatSnap. All rights reserved.Legal|Privacy policy|Modern Slavery Act Transparency Statement|Sitemap|About US| Contact US: help@patsnap.com