Wave springs for torsional vibration dampers
A technology of torsional shock absorber and wave spring, applied in the direction of spring, spring/shock absorber, cup spring, etc., can solve the problems of requiring axial structural space and affecting the structural space of clutch disc, etc.
- Summary
- Abstract
- Description
- Claims
- Application Information
AI Technical Summary
Problems solved by technology
Method used
Image
Examples
Embodiment Construction
[0034] figure 1 A schematic sectional view of a clutch disk 1 according to the invention with a torsional vibration damper 2 according to the invention is shown, wherein sub-figure A shows the radially inner second part of the torsional vibration damper 2 according to the invention. A sectional view of a spring set 4 , and sub-figure B shows a sectional view of its radially outer second spring set 6 . In this case, the radially inner spring set 4 defines a first pre-damper stage, and the radially outer spring set 6 defines a second pre-damper stage.
[0035] As is generally known, the clutch disk 1 is configured concentrically with respect to the axis of rotation D and has a hub 8 with internal toothing 10 for a non-rotatable mounting on a transmission shaft (not shown). On the outer circumference, the hub 8 has an external toothing 12 which carries the elements of the torsional vibration damper 2 for the idling system, the main torsional vibration damper 14 and the clutch di...
PUM
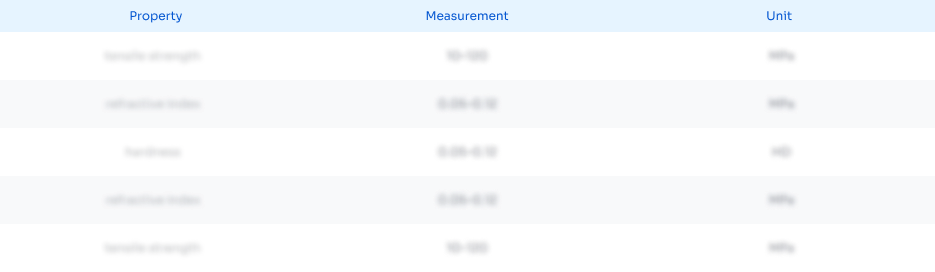
Abstract
Description
Claims
Application Information

- R&D
- Intellectual Property
- Life Sciences
- Materials
- Tech Scout
- Unparalleled Data Quality
- Higher Quality Content
- 60% Fewer Hallucinations
Browse by: Latest US Patents, China's latest patents, Technical Efficacy Thesaurus, Application Domain, Technology Topic, Popular Technical Reports.
© 2025 PatSnap. All rights reserved.Legal|Privacy policy|Modern Slavery Act Transparency Statement|Sitemap|About US| Contact US: help@patsnap.com