Production method for L-shaped unequal-wall-thickness profile
A production method, L-shaped technology, which is applied in the field of aluminum alloy extrusion production and wall thickness profile production, can solve the problems of affecting production rhythm, excessive deformation of profile thin-walled end gap, poor stability, etc., to improve production efficiency and mold service life , Dimensional accuracy and use performance are qualified, and the effect of high-precision extrusion production
- Summary
- Abstract
- Description
- Claims
- Application Information
AI Technical Summary
Problems solved by technology
Method used
Image
Examples
Embodiment Construction
[0021] The preferred embodiments of the present invention will be described in detail below in conjunction with the accompanying drawings; it should be understood that the preferred embodiments are only for illustrating the present invention, rather than limiting the protection scope of the present invention.
[0022] Such as figure 2 As shown in the production process flow, the present invention provides a production method for L-shaped profiles with unequal wall thickness, the main steps of which include: first, using the ingot as the original billet; then, sending the ingot into the extrusion molding process, Extruded into L-shaped profiles with unequal wall thickness, and obtained L-shaped finished extrusions by shearing; then, the L-shaped finished extrusions were sent to the cooling device for cooling; finally, the cooled L-shaped finished products were extruded The parts are sent to the roller pressing orthopedic process, and the final product is obtained after the ort...
PUM
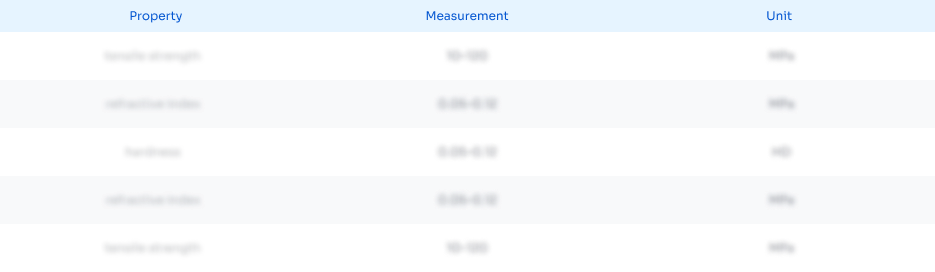
Abstract
Description
Claims
Application Information

- R&D
- Intellectual Property
- Life Sciences
- Materials
- Tech Scout
- Unparalleled Data Quality
- Higher Quality Content
- 60% Fewer Hallucinations
Browse by: Latest US Patents, China's latest patents, Technical Efficacy Thesaurus, Application Domain, Technology Topic, Popular Technical Reports.
© 2025 PatSnap. All rights reserved.Legal|Privacy policy|Modern Slavery Act Transparency Statement|Sitemap|About US| Contact US: help@patsnap.com