Configuration of hydraulic element of excavator
A technology for hydraulic components and excavators, which is applied to mechanically driven excavators/dredgers, earth movers/shovels, construction, etc., and can solve unreasonable internal oil passage design, large leakage, and large pressure loss, etc. problems, achieve the effect of optimizing the internal oil passage design, reducing energy waste and prolonging the service life
- Summary
- Abstract
- Description
- Claims
- Application Information
AI Technical Summary
Problems solved by technology
Method used
Image
Examples
Embodiment Construction
[0013] The present invention will be further described below in conjunction with the accompanying drawings and specific embodiments.
[0014] An excavator hydraulic component configuration, including a main pump 5, a swing motor 1 and a main control valve 3, the main pump 5 is connected to the engine 4 through the spline of the main shaft, and the main pump 5 and the main control valve 3 are connected through hydraulic pipelines The working oil port of the main control valve 3 is connected with the large and small cavities of each oil cylinder port of the excavator, the oil inlet and outlet ports of the rotary motor 1 and the travel motor, and the rotary motor 1 is a double rotary motor. The main pump 5 is a negative control series pump to provide working oil, with a displacement of 200ml / r; the rotary motor 1 is a fixed displacement dual motor with a displacement of 170ml / r; the main control valve 3 is a negative flow control valve, and the valve The core diameter is 34mm, th...
PUM
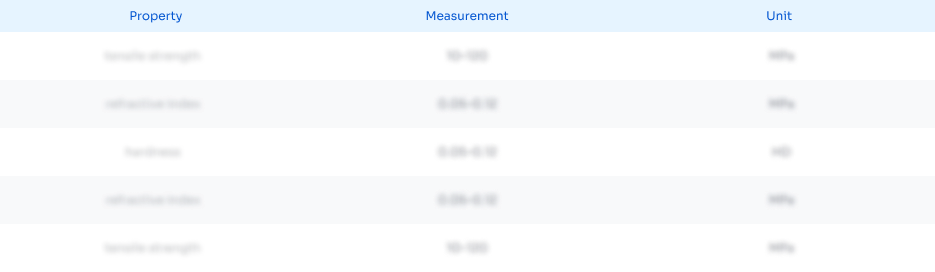
Abstract
Description
Claims
Application Information

- R&D Engineer
- R&D Manager
- IP Professional
- Industry Leading Data Capabilities
- Powerful AI technology
- Patent DNA Extraction
Browse by: Latest US Patents, China's latest patents, Technical Efficacy Thesaurus, Application Domain, Technology Topic, Popular Technical Reports.
© 2024 PatSnap. All rights reserved.Legal|Privacy policy|Modern Slavery Act Transparency Statement|Sitemap|About US| Contact US: help@patsnap.com