Planar positioning compensation method for motion platform system
A motion platform and plane positioning technology, which is applied in general control systems, control/adjustment systems, instruments, etc., can solve the change of compensation amount, two-dimensional compensation cannot meet the positioning accuracy requirements, and does not reflect the orthogonality error of the motion platform axis And other issues
- Summary
- Abstract
- Description
- Claims
- Application Information
AI Technical Summary
Problems solved by technology
Method used
Image
Examples
Embodiment Construction
[0009] The following discusses in detail the implementation and use of a specific embodiment of the plane positioning compensation method applying the motion platform system of the present invention. It should be understood, however, that the specific embodiments discussed are merely illustrative of specific ways to make and use the invention, and do not limit the scope of the invention.
[0010] The original data obtained by scanning the surface of the standard silicon wafer includes information such as the actual position of the motion platform, the recognized pattern pixel position, etc. The coordinate value of the recognized position of each pattern in the motion platform can be calculated from the position where the motion platform actually moves, the recognized pattern pixel position and the equivalent distance of each pixel.
[0011] Assuming that the coordinate system of the motion platform is the x, y axis, the relationship between it and the X, Y axis of the orthogon...
PUM
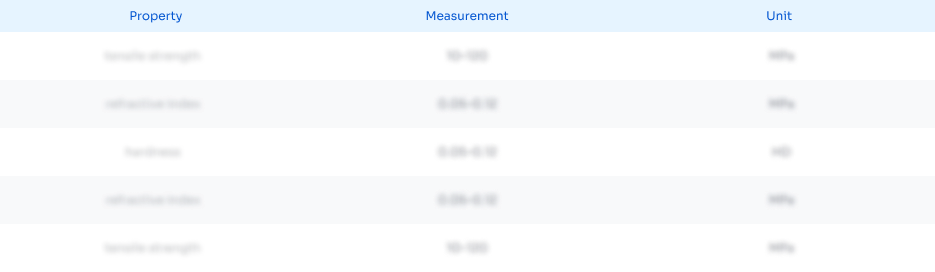
Abstract
Description
Claims
Application Information

- Generate Ideas
- Intellectual Property
- Life Sciences
- Materials
- Tech Scout
- Unparalleled Data Quality
- Higher Quality Content
- 60% Fewer Hallucinations
Browse by: Latest US Patents, China's latest patents, Technical Efficacy Thesaurus, Application Domain, Technology Topic, Popular Technical Reports.
© 2025 PatSnap. All rights reserved.Legal|Privacy policy|Modern Slavery Act Transparency Statement|Sitemap|About US| Contact US: help@patsnap.com