Calibration loading device for adjustable pretightened piezoelectric dynamometer through hydraulic pressure
A loading device and pre-tightening technology, applied in measuring devices, calibration/testing of force/torque/power measuring instruments, instruments, etc., can solve problems such as inability to evaluate errors, loss of meaning, and inability to calibrate multidimensional forces and moments. Achieve the effect of improving accuracy and reducing hysteresis
- Summary
- Abstract
- Description
- Claims
- Application Information
AI Technical Summary
Problems solved by technology
Method used
Image
Examples
Embodiment Construction
[0012] The implementation of the present invention will be described in detail in conjunction with the technical scheme and accompanying drawings. The loading cylinder liner 1 is fixed with bolts through the four equally divided stepped holes g on the cylinder body, and uses two positioning pin holes h to use the positioning pins to position the axis of the entire calibration loading device; the bottom of the loading cylinder liner 1 is processed with a The threaded hole 7 where the hydraulic joint is connected has a hydraulic joint sealing groove k for placing a sealing gasket to prevent oil leakage; a through hole m with a slightly smaller diameter is processed at the rear end of the hydraulic joint sealing groove k, and a diameter A circular anti-retraction groove l larger than the hole m, the end face f of the groove l is used as the installation and reset reference of the loading plunger 2; Shaped sealing groove, used to install the dynamic seal ring 6, through the contac...
PUM
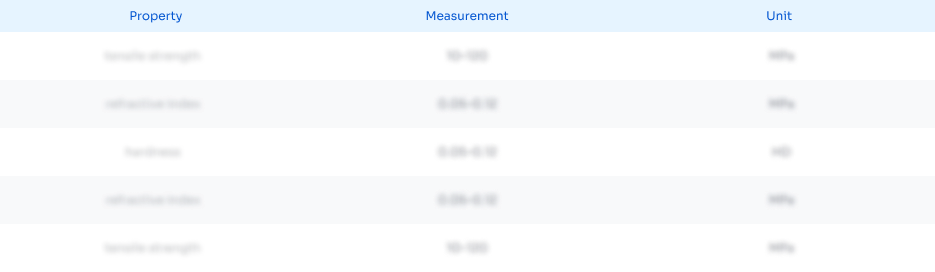
Abstract
Description
Claims
Application Information

- R&D
- Intellectual Property
- Life Sciences
- Materials
- Tech Scout
- Unparalleled Data Quality
- Higher Quality Content
- 60% Fewer Hallucinations
Browse by: Latest US Patents, China's latest patents, Technical Efficacy Thesaurus, Application Domain, Technology Topic, Popular Technical Reports.
© 2025 PatSnap. All rights reserved.Legal|Privacy policy|Modern Slavery Act Transparency Statement|Sitemap|About US| Contact US: help@patsnap.com