Shoe outsole material high in non-skid property
A technology for anti-skid performance and shoe outsole, which is applied in the field of shoe outsole materials, can solve the problems of hardening, anti-skid performance, poor wear resistance and cold resistance, and easy to slip, and achieves good wear resistance and cold resistance, guaranteeing Normal service life, good anti-skid performance
- Summary
- Abstract
- Description
- Claims
- Application Information
AI Technical Summary
Problems solved by technology
Method used
Examples
Embodiment 1
[0012] Embodiment one: the outsole material of shoes with good anti-skid performance, the outsole material of shoes is formulated by first material and second material, and following formula is according to weight ratio,
[0013] Ingredients of material A: 180 parts of polyurethane A material, 1 part of polyurethane C material front-stage catalyst, 1.5 parts of polyurethane C material rear-stage catalyst, 3 parts of anti-wear agent, 10 parts of color paste;
[0014] The process of preparing material A: heat polyurethane material A to 40 ℃ ~ 80 ℃, then keep warm to 45 ℃ ± 5 ℃, add polyurethane C material front-stage catalyst, polyurethane C material rear-stage catalyst, wear-resistant agent and color paste, Stir evenly to obtain material A with a temperature of 45°C±5°C and set aside;
[0015] B material composition: B material is 200 parts of polyurethane B material;
[0016] Preparation process of material B: heat material B to 40°C ~ 80°C, then keep warm to 45°C ± 5°C, and ...
Embodiment 2
[0019] Embodiment two: the outsole material of shoes with good anti-skid performance, the outsole material of shoes is formulated by first material and second material, and following formula is according to weight ratio,
[0020] Ingredients of material A: 180 parts of polyurethane A material, 2 parts of front-stage catalyst of polyurethane C material, 1 part of rear-stage catalyst of polyurethane C material, 1 part of anti-wear agent, 12 parts of color paste;
[0021] The process of preparing material A: heat polyurethane material A to 40 ℃ ~ 80 ℃, then keep warm to 45 ℃ ± 5 ℃, add polyurethane C material front-stage catalyst, polyurethane C material rear-stage catalyst, wear-resistant agent and color paste, Stir evenly to obtain material A with a temperature of 45°C±5°C and set aside;
[0022] B material composition: B material is 200 parts of polyurethane B material;
[0023] Preparation process of material B: heat material B to 40°C ~ 80°C, then keep warm to 45°C ± 5°C, a...
Embodiment 3
[0026] Embodiment three: the outsole material of shoes with good anti-skid property, the outsole material of shoes is formulated by first material and second material, and following formula is according to weight ratio,
[0027] Ingredients of material A: 180 parts of polyurethane A material, 1.5 parts of catalyst in the front stage of polyurethane C material, 1.25 parts of catalyst in the rear stage of polyurethane C material, 2 parts of anti-wear agent, 11 parts of color paste;
[0028] The process of preparing material A: heat polyurethane material A to 40 ℃ ~ 80 ℃, then keep warm to 45 ℃ ± 5 ℃, add polyurethane C material front-stage catalyst, polyurethane C material rear-stage catalyst, wear-resistant agent and color paste, Stir evenly to obtain material A with a temperature of 45°C±5°C and set aside;
[0029] B material composition: B material is 200 parts of polyurethane B material;
[0030] Preparation process of material B: heat material B to 40°C ~ 80°C, then keep w...
PUM
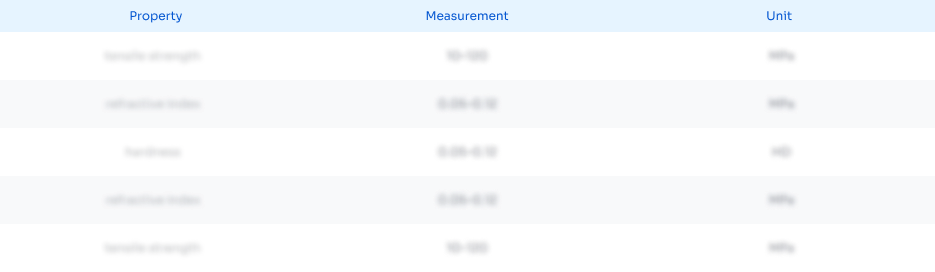
Abstract
Description
Claims
Application Information

- Generate Ideas
- Intellectual Property
- Life Sciences
- Materials
- Tech Scout
- Unparalleled Data Quality
- Higher Quality Content
- 60% Fewer Hallucinations
Browse by: Latest US Patents, China's latest patents, Technical Efficacy Thesaurus, Application Domain, Technology Topic, Popular Technical Reports.
© 2025 PatSnap. All rights reserved.Legal|Privacy policy|Modern Slavery Act Transparency Statement|Sitemap|About US| Contact US: help@patsnap.com