Ultrasonic sensor based method and system for recognition and positioning of fillet weld initial point
A starting point and sensor technology, applied in the field of automation, can solve problems such as inaccurate starting point positioning, low welding efficiency, and clamping errors, and achieve the effects of improving welding quality and welding efficiency, reducing labor intensity, and high system stability
- Summary
- Abstract
- Description
- Claims
- Application Information
AI Technical Summary
Problems solved by technology
Method used
Image
Examples
Embodiment 1
[0016] Embodiment 1 The present invention is based on the method and system for identifying and locating the starting point of the fillet weld with an ultrasonic sensor. The method and system are as follows: image 3 and Figure 4 As shown, it includes ultrasonic sensor 3, starting point recognition and positioning controller, driver, cross carriage (including horizontal carriage 1 and longitudinal carriage 2), among which cross carriage (including transverse carriage 1 and longitudinal carriage 2) with the workpiece mounted in a manner such as image 3 and Figure 4 As shown, the ultrasonic sensor 3 is rigidly fixed on the transverse carriage 1 and is in the same plane as the welding torch. The initial position recognition includes two parts: horizontal recognition and vertical recognition. For horizontal recognition, the motion model is as follows image 3 As shown, the ultrasonic sensor 3 is driven by the horizontal carriage 1 to scan the position, the ultrasonic sensor...
PUM
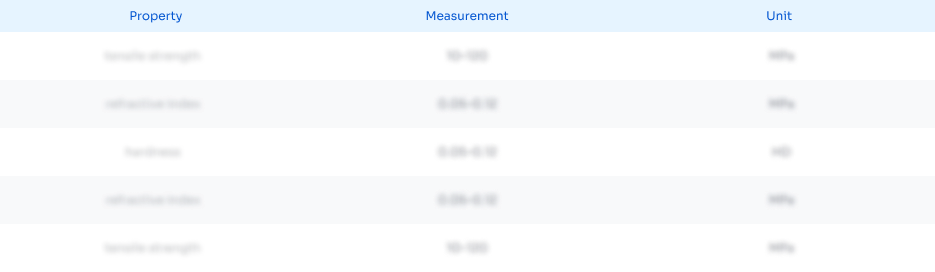
Abstract
Description
Claims
Application Information

- R&D
- Intellectual Property
- Life Sciences
- Materials
- Tech Scout
- Unparalleled Data Quality
- Higher Quality Content
- 60% Fewer Hallucinations
Browse by: Latest US Patents, China's latest patents, Technical Efficacy Thesaurus, Application Domain, Technology Topic, Popular Technical Reports.
© 2025 PatSnap. All rights reserved.Legal|Privacy policy|Modern Slavery Act Transparency Statement|Sitemap|About US| Contact US: help@patsnap.com