Multi-joint industrial mechanical arm
An industrial manipulator and multi-joint technology, applied in the direction of manipulators, program control manipulators, manufacturing tools, etc., can solve problems such as poor working stability, low service life, and prone to failure, so as to improve service life, high life, and provide accuracy Effect
- Summary
- Abstract
- Description
- Claims
- Application Information
AI Technical Summary
Problems solved by technology
Method used
Image
Examples
Embodiment Construction
[0046] The present invention will be further described below in conjunction with the accompanying drawings and specific embodiments.
[0047] Such as Figure 1-Figure 5 As shown, the multi-joint industrial manipulator provided in this embodiment includes a base 10 that can be fixed on the bottom plate and a control system for controlling the movement of the entire manipulator. The control system is a conventional system in the art and will not be described in detail here.
[0048]A first joint 20 and a first driving device 30 for driving the first joint 20 to rotate are installed on the base 10 . The first joint 20 is installed on the upper end of the base 10, and the first driving device 30 includes a first motor 31 located inside the base 10 and a first speed reducer 32 connected to the first motor 31, and the output shaft of the first motor 31 Arranged vertically, the output shaft of the first reducer 32 is coaxial with the output shaft of the first motor 31, and the first...
PUM
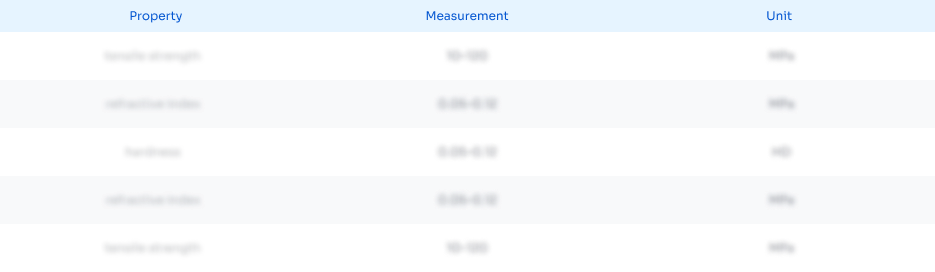
Abstract
Description
Claims
Application Information

- R&D
- Intellectual Property
- Life Sciences
- Materials
- Tech Scout
- Unparalleled Data Quality
- Higher Quality Content
- 60% Fewer Hallucinations
Browse by: Latest US Patents, China's latest patents, Technical Efficacy Thesaurus, Application Domain, Technology Topic, Popular Technical Reports.
© 2025 PatSnap. All rights reserved.Legal|Privacy policy|Modern Slavery Act Transparency Statement|Sitemap|About US| Contact US: help@patsnap.com