Modeling method of dispersed-phase reinforced composite material meso-structure
A technology for reinforced composite materials and modeling methods, which is applied in the modeling of particle-reinforced and short-fiber-reinforced composite mesostructures, and the modeling of discrete-phase reinforced composite mesostructures, which can solve the problem of insufficient reinforced phase density, etc. problem, to achieve the effect of easy control of distribution density, uniformity, and short calculation time.
- Summary
- Abstract
- Description
- Claims
- Application Information
AI Technical Summary
Problems solved by technology
Method used
Image
Examples
Embodiment 1
[0046] like figure 1 Shown: A modeling method for the three-dimensional mesostructure of particle-reinforced composite materials, including the following steps:
[0047] (1) Draw up the shape and size of the composite material model, and determine the model boundary;
[0048] (2) formulate the volume sum of the particle-reinforced phase in each size range in the model, that is, set the volume sum of the particle-reinforced phase in the i size range as V(i);
[0049] (3) In the model space 3 and the space 2 above the model, randomly obtain several particle models 1 within the size range of i, so that the volume sum of each particle model 1 is V(i), and each particle model 1 is Leave a gap with the surrounding model;
[0050] The method for obtaining several particle models 1 within the size range of i comprises the following steps:
[0051] a. In the model space 3 and the space 2 above the model, randomly generate a point, and use this point as the center to generate a ball wi...
Embodiment 2
[0064] like Figure 4 As shown, a modeling method for the two-dimensional mesostructure of particle reinforced composites includes the following steps:
[0065] (1) Draw up the shape and size of the composite material model, and determine the model boundary;
[0066] (2) Draw up the area sum of the particle-reinforced phase in each size range in the model, that is, set the area sum of the particle-reinforced phase in the i size range as S(i);
[0067] (3) In the model space 3 and the space 2 above the model, randomly obtain several particle models 1 within the size range of i, so that the area sum of each particle model is S(i), and each particle model is consistent with the surrounding There are gaps between the models;
[0068] The method for obtaining several particle models 1 within the size range of i comprises the following steps:
[0069] a. In the model space 3 and the space 2 above the model, randomly generate a point, and use this point as the center to generate a...
Embodiment 3
[0082] A modeling method for the mesostructure of a fiber reinforced composite material, comprising the following steps:
[0083] (1) Draw up the shape and size of the composite material model, and determine the model boundary;
[0084] (2) Formulate the volume sum of the fiber-reinforced phases in each size range in the model, that is, set the volume sum of the fiber-reinforced phases whose diameter is in the i-size range and whose length is in the j-size range as V(i,j) ;
[0085] (3) In the model and the space above it, randomly obtain several fiber models within the size range of i and j, so that the volume sum of each fiber model is V(i, j), and each fiber model is consistent with the surrounding There are gaps between the models;
[0086] The method for obtaining several fiber models within the size range of i and j comprises the following steps:
[0087] a. In the model and the space above it, randomly generate a point, centering on this point, generate a cylinder wi...
PUM
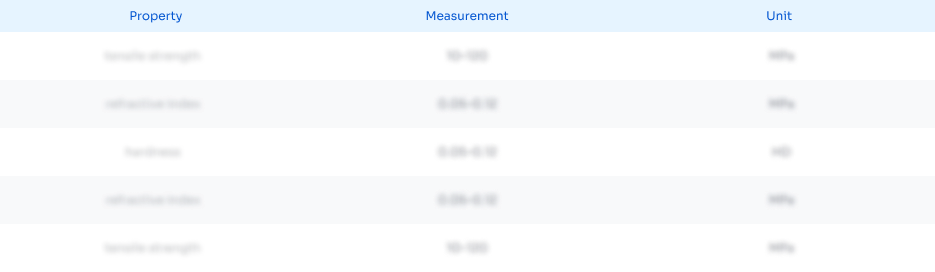
Abstract
Description
Claims
Application Information

- R&D
- Intellectual Property
- Life Sciences
- Materials
- Tech Scout
- Unparalleled Data Quality
- Higher Quality Content
- 60% Fewer Hallucinations
Browse by: Latest US Patents, China's latest patents, Technical Efficacy Thesaurus, Application Domain, Technology Topic, Popular Technical Reports.
© 2025 PatSnap. All rights reserved.Legal|Privacy policy|Modern Slavery Act Transparency Statement|Sitemap|About US| Contact US: help@patsnap.com