Cast welding die for busbar of storage battery
A technology for casting and welding molds and busbars, which is applied to the field of casting and welding molds for battery busbars, can solve problems such as low work efficiency, and achieve the effects of improving production efficiency, simple overall structure, and accelerating cooling speed.
- Summary
- Abstract
- Description
- Claims
- Application Information
AI Technical Summary
Problems solved by technology
Method used
Image
Examples
Embodiment Construction
[0022] The present invention will be further described below in conjunction with the accompanying drawings and specific embodiments.
[0023] As shown in the figure, the battery busbar casting and welding mold provided by the embodiment of the present invention includes a mold body 1. The upper surface of the mold body is provided with multiple groups of molding units for casting battery busbars. The molding units include positive electrode concaves arranged side by side. Road 11 and negative groove 12.
[0024] It also includes a scraper 8 arranged on the top of the mold body, the top of the scraper is provided with a shaft 81, and the four corners of the mold body 1 are fixed with upward brackets 6, and the top of the bracket is fixed with two blades with the length of the mold body. The ejector rod 9 in the same direction is provided with a groove 91 adapted to the shaft along its length direction, and a heat-insulating end sleeve 82 is provided at the end of the shaft prot...
PUM
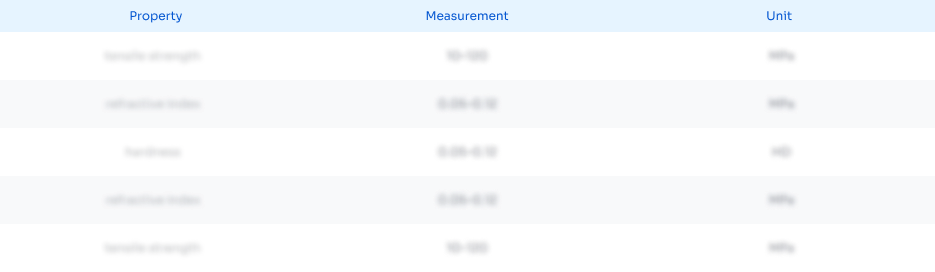
Abstract
Description
Claims
Application Information

- R&D Engineer
- R&D Manager
- IP Professional
- Industry Leading Data Capabilities
- Powerful AI technology
- Patent DNA Extraction
Browse by: Latest US Patents, China's latest patents, Technical Efficacy Thesaurus, Application Domain, Technology Topic, Popular Technical Reports.
© 2024 PatSnap. All rights reserved.Legal|Privacy policy|Modern Slavery Act Transparency Statement|Sitemap|About US| Contact US: help@patsnap.com