Automatic calibration method of robot system
A robot system and automatic calibration technology, applied in general control systems, control/regulation systems, instruments, etc., can solve problems such as troublesome, inaccurate calibration, and time-consuming, and achieve the effects of high efficiency, improved calibration accuracy, and convenient calibration.
- Summary
- Abstract
- Description
- Claims
- Application Information
AI Technical Summary
Problems solved by technology
Method used
Image
Examples
Embodiment Construction
[0039] The technical solutions of the present invention will be further specifically described below through the embodiments and in conjunction with the accompanying drawings. In the specification, the same or similar reference numerals designate the same or similar components. The following description of the embodiments of the present invention with reference to the accompanying drawings is intended to explain the general inventive concept of the present invention, but should not be construed as a limitation of the present invention.
[0040] figure 1 A three-dimensional schematic diagram of a robot system according to an exemplary embodiment of the present invention is shown.
[0041] figure 1 A schematic diagram of a six-axis robot system is shown, however, the present invention is not limited to the illustrated embodiment, and the robot system may also be other types of multi-degree-of-freedom robot systems, for example, a four-axis robot system or a five-axis robot sys...
PUM
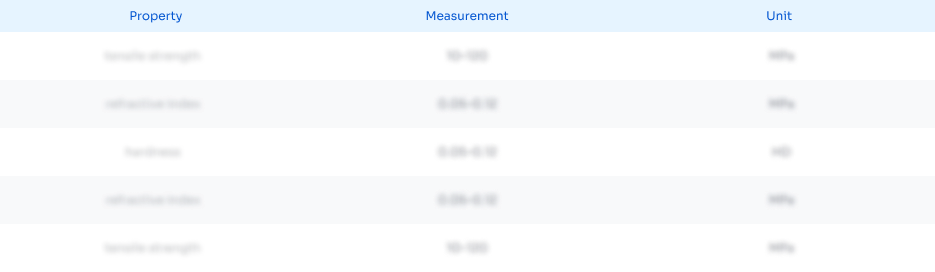
Abstract
Description
Claims
Application Information

- Generate Ideas
- Intellectual Property
- Life Sciences
- Materials
- Tech Scout
- Unparalleled Data Quality
- Higher Quality Content
- 60% Fewer Hallucinations
Browse by: Latest US Patents, China's latest patents, Technical Efficacy Thesaurus, Application Domain, Technology Topic, Popular Technical Reports.
© 2025 PatSnap. All rights reserved.Legal|Privacy policy|Modern Slavery Act Transparency Statement|Sitemap|About US| Contact US: help@patsnap.com