A Method for Determining Dynamic Parameters of Cracked Gear-Rotor System Considering Extended Meshing
A gear rotor, parameter determination technology, applied in electrical digital data processing, special data processing applications, instruments, etc., can solve the problems of early meshing, extended meshing, and high time-varying meshing stiffness
- Summary
- Abstract
- Description
- Claims
- Application Information
AI Technical Summary
Problems solved by technology
Method used
Image
Examples
Embodiment Construction
[0071] The specific embodiments of the present invention will be described in detail below in conjunction with the accompanying drawings.
[0072] A method for determining the dynamic parameters of a cracked gear-rotor system considering extended meshing, such as figure 1 shown, including the following steps:
[0073] Step 1: Obtain the basic parameters of the healthy gear and the basic parameters and crack parameters of the cracked gear.
[0074] In this embodiment, the basic parameters of the healthy gear and the basic parameters of the cracked gear are obtained as shown in Table 1:
[0075] Table 1 Basic parameters of healthy gears and basic parameters of cracked gears
[0076]
[0077] Schematic diagram of crack gear figure 2 Shown: the geometric parameters of the crack (q, υ, ψ), where q represents the depth of the crack, υ represents the direction of crack propagation, ψ represents the starting position of the crack, G is the intersection point of the addendum cir...
PUM
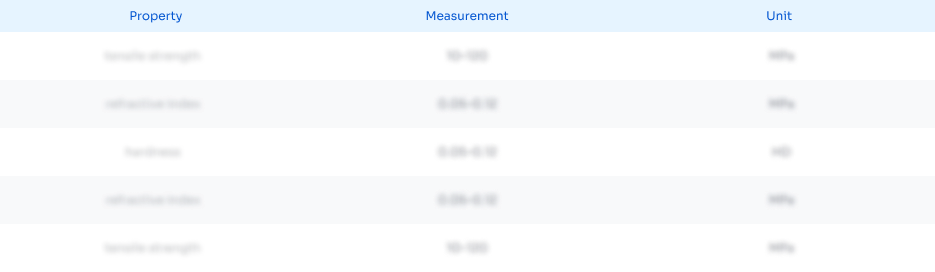
Abstract
Description
Claims
Application Information

- R&D
- Intellectual Property
- Life Sciences
- Materials
- Tech Scout
- Unparalleled Data Quality
- Higher Quality Content
- 60% Fewer Hallucinations
Browse by: Latest US Patents, China's latest patents, Technical Efficacy Thesaurus, Application Domain, Technology Topic, Popular Technical Reports.
© 2025 PatSnap. All rights reserved.Legal|Privacy policy|Modern Slavery Act Transparency Statement|Sitemap|About US| Contact US: help@patsnap.com