Leveling method for multi-shaft support air-floating platform based on capacitive sensors
A technology of capacitive sensors and air-floating platforms, which is applied in the direction of supporting machines, machines/supports, and feedback control, can solve the problems of high adjustment accuracy, low adjustment process complexity, and large application limitations, and achieve anti-interference Powerful, quick and easy to apply effects
- Summary
- Abstract
- Description
- Claims
- Application Information
AI Technical Summary
Problems solved by technology
Method used
Image
Examples
specific Embodiment approach 1
[0024] Specific implementation mode one: the following combination figure 1 Describe this embodiment, the leveling method of the capacitive sensor-based multi-axis supported air bearing platform described in this embodiment, the specific process of the leveling method is:
[0025] Step 1. The gas source is filled with high-pressure gas at the bottom of the three gas feet to form a gas film surface;
[0026] Step 2, using three capacitive sensors to collect the air film heights of the three air feet respectively;
[0027] Step 3, the three capacitive sensors respectively output the collected air film height to the controller;
[0028] Step 4, the controller uses the neural network PID control algorithm to calculate the control quantity;
[0029] Step 5. After decoupling the control volume, control the pressure regulating valves of the three air feet, change the outlet pressure of the three air feet, adjust the height of the air film, and complete the leveling process.
specific Embodiment approach 2
[0030] Specific implementation mode two: this implementation mode further explains implementation mode one, and the specific method for calculating the control amount described in step 4 is:
[0031] u ( k ) = u ( k - 1 ) + K Σ i = 1 3 ( w i ( k ) / Σ i = 1 3 | w i ( k ) | ) x i ( ...
PUM
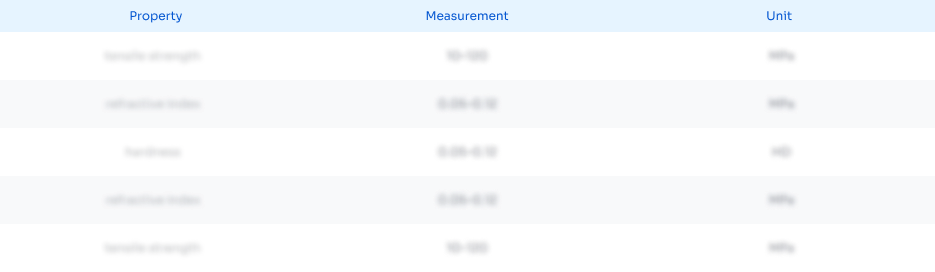
Abstract
Description
Claims
Application Information

- R&D Engineer
- R&D Manager
- IP Professional
- Industry Leading Data Capabilities
- Powerful AI technology
- Patent DNA Extraction
Browse by: Latest US Patents, China's latest patents, Technical Efficacy Thesaurus, Application Domain, Technology Topic, Popular Technical Reports.
© 2024 PatSnap. All rights reserved.Legal|Privacy policy|Modern Slavery Act Transparency Statement|Sitemap|About US| Contact US: help@patsnap.com