A stamping method and equipment for producing fiber-reinforced composite material preform
A technology of stamping equipment and composite materials, which is applied in the field of stamping and equipment for the production of fiber-reinforced composite material preforms. It can solve the problems of reducing the production cost of composite material parts and the inapplicability of fiber laying technology, and achieves a high degree of automation. Cost, product The effect of quality assurance and low error rate
- Summary
- Abstract
- Description
- Claims
- Application Information
AI Technical Summary
Problems solved by technology
Method used
Image
Examples
Embodiment Construction
[0034] The application will be further explained below in conjunction with the accompanying drawings.
[0035] The stamping equipment used to produce fiber-reinforced composite material preforms provided by this application has a basic structure as follows: figure 2 As shown, it includes a support 1, a column 2 on the support, a motor 3, a crankshaft 4, a total stamping block 5, an upper module 6, a lower module 7, and an upper fixed slideway 8 and a lower fixed slideway 9. The upper fixed slideway 8 and the lower fixed slideway 9 are respectively connected with the upper module 6 and the lower module 7, wherein the upper fixed slideway 8 is fixed on the upper end of the support 1 and below the column 2, and the lower fixed slideway 9 is located at the bottom of the support 1, It can also be fixed on the ground, and the support frame 21 can be clamped by a mechanical arm clamp for easy transportation. During the stamping process, the support frame 21 is fixed on the frame 1 ...
PUM
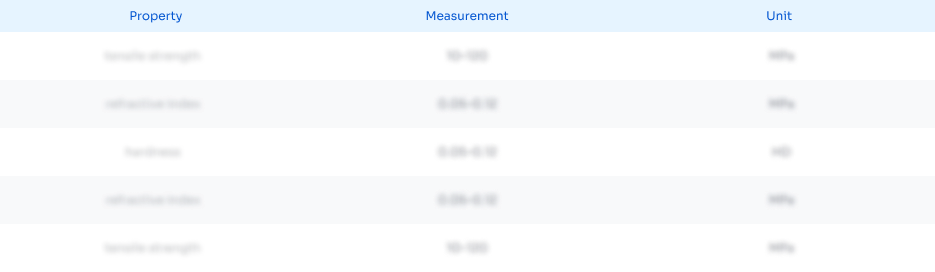
Abstract
Description
Claims
Application Information

- R&D Engineer
- R&D Manager
- IP Professional
- Industry Leading Data Capabilities
- Powerful AI technology
- Patent DNA Extraction
Browse by: Latest US Patents, China's latest patents, Technical Efficacy Thesaurus, Application Domain, Technology Topic, Popular Technical Reports.
© 2024 PatSnap. All rights reserved.Legal|Privacy policy|Modern Slavery Act Transparency Statement|Sitemap|About US| Contact US: help@patsnap.com