Electromagnetic tracking system and method based on rapid determination of vector rotation angle of maximum magnetic induction intensity
A technology of magnetic induction intensity and vector rotation, applied in the field of electromagnetic tracking, can solve the problems of poor real-time performance of the system and poor search flexibility, and achieve the effects of avoiding positioning errors, improving positioning speed, and avoiding system instability
- Summary
- Abstract
- Description
- Claims
- Application Information
AI Technical Summary
Problems solved by technology
Method used
Image
Examples
Embodiment Construction
[0075]The composition and working process of the system will be described below in conjunction with specific embodiments and with reference to the accompanying drawings. The coordinate system definition involved in this specific embodiment is the same as Table 1, as Figure 7 Shown; The definition of the horizontal rotation angle and vertical rotation angle involved is the same as the content of the invention.
[0076] This specific embodiment designs figure 1 The electromagnetic tracking system 1 shown includes four parts: a three-axis magnetic field sensor device 2 , a magnetic field source device 3 , a control processing display device 4 , and a controllable constant current source device 5 . The three-axis magnetic field sensor device 2 is attached to the tracking target. The magnetic field source device 3 includes two magnetic field sources 10 and 11 (corresponding to the magnetic field source 1 and the magnetic field source 2 described in the summary of the invention ...
PUM
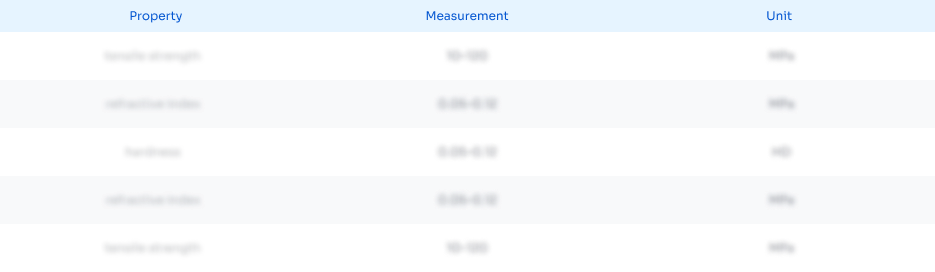
Abstract
Description
Claims
Application Information

- R&D
- Intellectual Property
- Life Sciences
- Materials
- Tech Scout
- Unparalleled Data Quality
- Higher Quality Content
- 60% Fewer Hallucinations
Browse by: Latest US Patents, China's latest patents, Technical Efficacy Thesaurus, Application Domain, Technology Topic, Popular Technical Reports.
© 2025 PatSnap. All rights reserved.Legal|Privacy policy|Modern Slavery Act Transparency Statement|Sitemap|About US| Contact US: help@patsnap.com