Test tube rack for analyzer assembly line and displacement detection method and device of test tube rack
A test tube rack and analyzer technology, used in measuring devices, test tube supports/clamps, analytical materials, etc., can solve problems such as false pulses, missed detection, widening the gap between groove signals and edge signals, and meet performance requirements. The effect of reducing, reducing cost and improving reliability
- Summary
- Abstract
- Description
- Claims
- Application Information
AI Technical Summary
Problems solved by technology
Method used
Image
Examples
Embodiment 1
[0034] Please refer to image 3 , this embodiment provides a test tube rack for an analyzer assembly line, the test tube rack is provided with a plurality of test tube positions for accommodating test tubes 301, and one side of the test tube rack (for example, the side facing the light sensor) is provided with The light blocking plate 300 of the position, the second characteristic area 303 is arranged between two adjacent test tube positions on the light blocking plate 300, the first characteristic area 302 is between the adjacent two second characteristic areas 303, the first characteristic area 302 and the second characteristic area 303 have a step difference with a preset depth. The first characteristic regions 302 and the second characteristic regions 303 are arranged alternately and evenly on the light blocking plate 300 .
[0035] In a specific embodiment, the second characteristic region 303 is a groove with a predetermined depth lower than the first characteristic reg...
Embodiment 2
[0043] Please refer to Figure 5 , based on the test tube rack of the analyzer assembly line provided in Embodiment 1, this embodiment provides a method for detecting displacement of the test tube rack correspondingly, including:
[0044] Step 501: Obtain the detection signal output by the sensor during a single displacement of the test tube rack. The shifting of the test tube rack from the start to the stop is a single shift.
[0045] Step 502: Amplify and digitally filter the detection signal to eliminate the interference of noise, local potholes and uneven factors on the surface of the test tube rack, and obtain a more realistic signal. Specifically, a median filtering algorithm may be selected for digital filtering.
[0046] Step 503: Obtain the initial voltage V_ORI at the beginning of the test tube rack shift, the end voltage V_END at the end of the shift, and the maximum voltage V_EXT between the initial shift and the end of the shift from the digitally filtered signa...
Embodiment 3
[0068] Please refer to Figure 8 , based on the test tube rack displacement detection method provided in Embodiment 2, this embodiment provides a device for detecting the test tube rack displacement of the analyzer assembly line. In a specific example, the device for detecting the test tube rack displacement includes features A voltage acquisition module 601 and a shift judgment module 602 .
[0069] The characteristic voltage acquisition module 601 is used to obtain the detection signal output by the sensor during a single shift of the test tube rack, and obtain the end voltage at the end of the test tube rack shift and the maximum value between the initial shift and the end of the shift from the detection signal Voltage.
[0070] The shift judging module 602 is used to judge whether the ratio of the maximum voltage to the end voltage satisfies the first judging condition. If so, it is judged that the test tube rack is shifted correctly; otherwise, it is judged that the test...
PUM
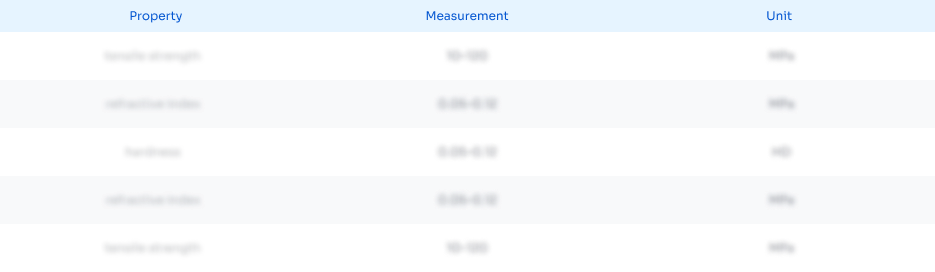
Abstract
Description
Claims
Application Information

- R&D Engineer
- R&D Manager
- IP Professional
- Industry Leading Data Capabilities
- Powerful AI technology
- Patent DNA Extraction
Browse by: Latest US Patents, China's latest patents, Technical Efficacy Thesaurus, Application Domain, Technology Topic, Popular Technical Reports.
© 2024 PatSnap. All rights reserved.Legal|Privacy policy|Modern Slavery Act Transparency Statement|Sitemap|About US| Contact US: help@patsnap.com