Complex surface numerical control machining motion analyzing method based on mapping
A technology for complex curved surfaces and machining motion, applied in the directions of digital control, program control, electrical program control, etc., can solve problems such as inability to perform forward-looking analysis, large consumption of computing resources, etc., to facilitate software integration and practical application, and achieve large engineering value. Effect
- Summary
- Abstract
- Description
- Claims
- Application Information
AI Technical Summary
Problems solved by technology
Method used
Image
Examples
Embodiment Construction
[0027] specific implementation plan
[0028] In the following, specific embodiments of the present invention will be described in detail in combination with technical solutions and accompanying drawings, and detailed implementation methods and processes will be given, but the scope of protection of the present invention is not limited to the following embodiments.
[0029] Step 1. Parametric expression of general inclined plane machining
[0030] The processing of any inclined plane is regarded as a processing type in which the tool axis is vertical, the tool is in translation, and the workpiece is in angular swing, so that two basic independent variables, the inclination angle of the inclined plane and the feed direction angle, are abstracted. Such as figure 1 As shown, the inclination angle of the bevel is defined as the angle between the normal direction of the bevel and the tool axis vector, and its expression is shown in formula 1. The feed direction angle is defined as...
PUM
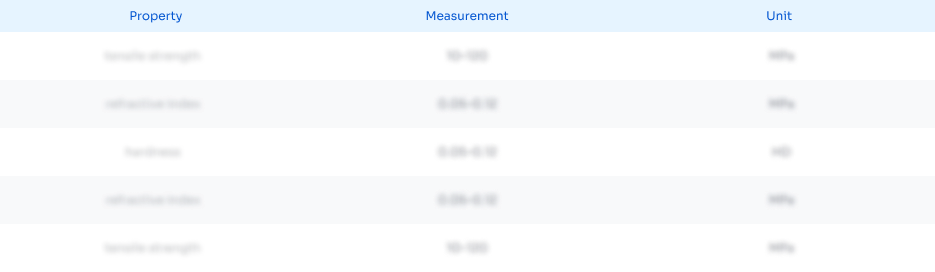
Abstract
Description
Claims
Application Information

- R&D
- Intellectual Property
- Life Sciences
- Materials
- Tech Scout
- Unparalleled Data Quality
- Higher Quality Content
- 60% Fewer Hallucinations
Browse by: Latest US Patents, China's latest patents, Technical Efficacy Thesaurus, Application Domain, Technology Topic, Popular Technical Reports.
© 2025 PatSnap. All rights reserved.Legal|Privacy policy|Modern Slavery Act Transparency Statement|Sitemap|About US| Contact US: help@patsnap.com