Rotor system fault diagnosis method and device based on vibration analysis
A system failure and vibration analysis technology, applied in the direction of measuring devices, testing of mechanical components, testing of machine/structural components, etc., can solve problems such as modal confusion, over-envelope, and affecting the accuracy of fault diagnosis, and achieve rapid and accurate identification , The effect of alleviating the problem of error accumulation
- Summary
- Abstract
- Description
- Claims
- Application Information
AI Technical Summary
Problems solved by technology
Method used
Image
Examples
specific example
[0078] This example uses Figure 5 The experimental data of the rotor test bench shown is verified. The test bench is based on the low-pressure rotor system of the PW4000 twin-rotor turbofan engine, and adopts the same 0-2-1 support structure and bearing type as the original machine. The test bench size It is twice the size of the model and driven by a motor.
[0079] Step 1: Use the vibration displacement sensor to collect 20 sets of signals for each of the normal, slight misalignment, severe misalignment, rubbing, and bearing rolling element faults of the rotor system. A total of 100 sets of signals are obtained. The sampling frequency is 20kHz, and the vibration signals of the five states of the rotor system are obtained. Such as Figure 2a , Figure 2b , Figure 2c , Figure 2d and Figure 2e shown. Among them, the misalignment fault is realized by adjusting the support height of the bearing seat, the rubbing fault is realized by the rubbing device, and the bearing f...
PUM
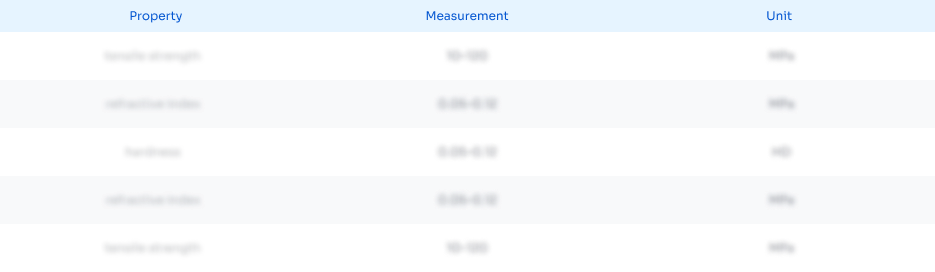
Abstract
Description
Claims
Application Information

- R&D
- Intellectual Property
- Life Sciences
- Materials
- Tech Scout
- Unparalleled Data Quality
- Higher Quality Content
- 60% Fewer Hallucinations
Browse by: Latest US Patents, China's latest patents, Technical Efficacy Thesaurus, Application Domain, Technology Topic, Popular Technical Reports.
© 2025 PatSnap. All rights reserved.Legal|Privacy policy|Modern Slavery Act Transparency Statement|Sitemap|About US| Contact US: help@patsnap.com