Kiln residual heat system capable of automatically controlling auxiliary heating equipment to be started
A kiln and waste heat technology, applied in lighting and heating equipment, heating systems, hot water central heating systems, etc., to enhance heat transfer and avoid low-temperature corrosion
- Summary
- Abstract
- Description
- Claims
- Application Information
AI Technical Summary
Problems solved by technology
Method used
Image
Examples
Embodiment Construction
[0042] The specific embodiments of the present invention will be described in detail below in conjunction with the accompanying drawings.
[0043] Such as Figure 1-2 As shown, a cogeneration system of heat and power includes a waste heat system, a heat exchange system and a heat dissipation system, wherein the heat exchange relationship between the waste heat system and the heat exchange system is carried out through an air-water heat exchanger 6, and the heat exchange system and the heat dissipation system are passed through A heat exchanger 13 is connected for heat exchange.
[0044] figure 1 A kiln waste heat utilization system is shown, the system includes a kiln 1, a main flue 37, a bypass flue 38 and an air-water heat exchanger 6, and the flue gas generated by the kiln passes through the bypass flue inlet 39 After entering the air-water heat exchanger 6, the flue gas after heat exchange flows into the main flue 37 through the outlet 40 of the bypass flue and then is d...
PUM
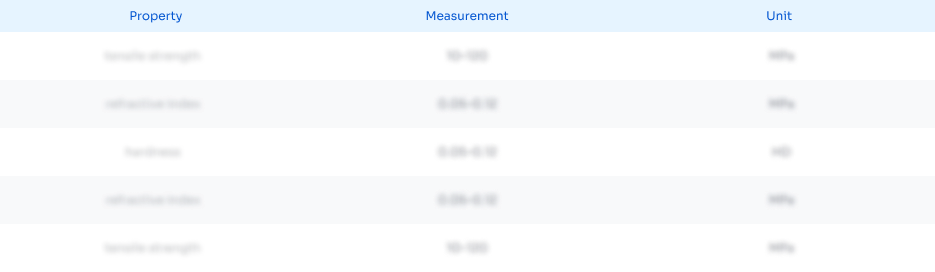
Abstract
Description
Claims
Application Information

- R&D
- Intellectual Property
- Life Sciences
- Materials
- Tech Scout
- Unparalleled Data Quality
- Higher Quality Content
- 60% Fewer Hallucinations
Browse by: Latest US Patents, China's latest patents, Technical Efficacy Thesaurus, Application Domain, Technology Topic, Popular Technical Reports.
© 2025 PatSnap. All rights reserved.Legal|Privacy policy|Modern Slavery Act Transparency Statement|Sitemap|About US| Contact US: help@patsnap.com