In-mold riveting automatic feeding mechanism
An automatic feeding and in-mold riveting technology, applied in the field of in-mold riveting automatic feeding mechanism, can solve the problems of high manufacturing cost and use cost, low production efficiency, easy failure, etc., and achieve low failure, high production efficiency and riveting accuracy high effect
- Summary
- Abstract
- Description
- Claims
- Application Information
AI Technical Summary
Problems solved by technology
Method used
Image
Examples
Embodiment
[0018] Embodiment: an automatic feeding mechanism for in-mold riveting, including stamping upper die 1, stamping lower die 2, vibrating plate 3, supporting plate 4, vibrating plate driving device, rivet baffle plate 5, positioning pin 6 and positioning pin driving device, The stamping upper die 1 can be reciprocated longitudinally and positioned directly above the stamping lower die 2, the positioning pin 6 can be vertically lifted and inserted in the stamping lower die 2, the positioning pin driving device drives the positioning pin 6 to move vertically, and the supporting plate 4. It is fixedly positioned on the outside of the stamping lower die 2. The vibrating plate 3 can slide back and forth toward the inner direction of the stamping upper die and the stamping lower die and is positioned on the supporting plate 4. The rivet at the end of the vibrating disc discharge channel 8 can be coaxially aligned with the positioning pin 6. Yes, the rivet baffle 5 is positioned and ins...
PUM
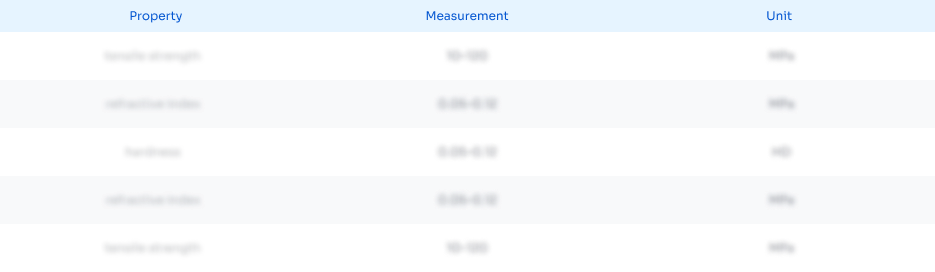
Abstract
Description
Claims
Application Information

- Generate Ideas
- Intellectual Property
- Life Sciences
- Materials
- Tech Scout
- Unparalleled Data Quality
- Higher Quality Content
- 60% Fewer Hallucinations
Browse by: Latest US Patents, China's latest patents, Technical Efficacy Thesaurus, Application Domain, Technology Topic, Popular Technical Reports.
© 2025 PatSnap. All rights reserved.Legal|Privacy policy|Modern Slavery Act Transparency Statement|Sitemap|About US| Contact US: help@patsnap.com