Three-dimensional oil-water separation material based on electrospinning technology and its preparation method
An electrospinning technology and oil-water separation technology, which is applied in the field of three-dimensional oil-water separation materials and their preparation, can solve the problems of no mechanical elasticity, low oil absorption rate, and difficulty in maintaining oil, and achieve the effects of improving performance, high oil absorption rate, and low density.
- Summary
- Abstract
- Description
- Claims
- Application Information
AI Technical Summary
Problems solved by technology
Method used
Image
Examples
Embodiment 1
[0026] 1) Preparation of spinning solution: Weigh 2 g of polyacrylonitrile (PAN) powder and 0.3 g of graphene oxide (GO) into a 100 mL conical flask containing 20 g of dimethylformamide (DMF) solvent placed in a water bath at 60 °C, heated and stirred until dissolved, and configured as a PAN-GO mixed solution.
[0027] 2) Preparation of nanofibers: The electrospinning solution in step 1) was placed in a 10 ml syringe, and the nanofibers were collected in a plastic container filled with water as a nanofiber receiver. Spinning parameters are: voltage 15 kV, spinneret inner diameter 0.6 mm, spinning solution flow rate 0.9 mL / h, distance from spinneret to receiving water surface 15 cm, receiving time 3 h, ambient conditions: temperature 30±5°C , the relative humidity is 50±5%, and the receiver moves back and forth at a speed of 0.2 cm / s.
[0028] 3) Preparation of three-dimensional nanofibers: The nanofiber solution collected in step 2 was evenly dispersed and shaped into a beake...
Embodiment 2
[0032] 1) Preparation of spinning solution: Weigh 2 g of polyacrylonitrile (PAN) powder, add it into a 100 mL Erlenmeyer flask containing 20 g of dimethylformamide (DMF) solvent, and heat it in a water bath at 60 °C Stir until dissolved and configure as a PAN mixed solution.
[0033] 2) Preparation of nanofibers: The electrospinning solution in step 1) was placed in a 10 ml syringe, and the nanofibers were collected in a plastic container filled with water as a nanofiber receiver. Spinning parameters are: voltage 15 kV, spinneret inner diameter 0.6 mm, spinning solution flow rate 0.9 mL / h, distance from spinneret to receiving water surface 15 cm, receiving time 3 h, ambient conditions: temperature 30±5°C , the relative humidity is 50±5%, and the receiver moves back and forth at a speed of 0.1 cm / s.
[0034] 3) Preparation of three-dimensional nanofibers: add 0.2 g graphene oxide and 0.2 g dopamine to the nanofiber solution collected in step 2, react for 24 h, shape it in a be...
Embodiment 3
[0039] 1) Preparation of spinning solution: Weigh 2 g of polyacrylonitrile (PAN) powder and 0.5 g of hydrophobic nano-silica ions (SiO 2 ), added to a 100 mL Erlenmeyer flask containing 20 g of dimethylformamide (DMF) solvent, heated and stirred in a water bath at 60°C until dissolved, and configured as PAN-SiO 2 mixture.
[0040] 2) Preparation of nanofibers: The electrospinning solution in step 1) was placed in a 10 ml syringe, and the nanofibers were collected in a plastic container filled with water as a nanofiber receiver. Spinning parameters are: voltage 15 kV, spinneret inner diameter 0.6 mm, spinning solution flow rate 0.9 mL / h, distance from spinneret to receiving water surface 15 cm, receiving time 3 h, ambient conditions: temperature 30±5°C , the relative humidity is 50±5%, and the receiver moves back and forth at a speed of 0.2 cm / s.
[0041]3) Preparation of three-dimensional nanofibers: fully disperse and shape the nanofiber solution collected in step 2 into a ...
PUM
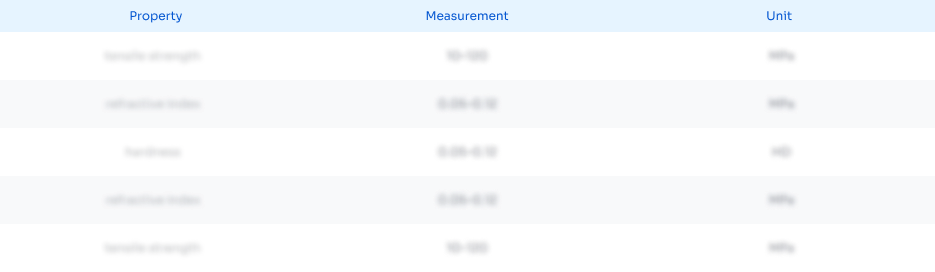
Abstract
Description
Claims
Application Information

- R&D
- Intellectual Property
- Life Sciences
- Materials
- Tech Scout
- Unparalleled Data Quality
- Higher Quality Content
- 60% Fewer Hallucinations
Browse by: Latest US Patents, China's latest patents, Technical Efficacy Thesaurus, Application Domain, Technology Topic, Popular Technical Reports.
© 2025 PatSnap. All rights reserved.Legal|Privacy policy|Modern Slavery Act Transparency Statement|Sitemap|About US| Contact US: help@patsnap.com