Full-automatic winding device and winding displacement control method thereof
A technology of winding device and control method, which is applied in the control field of automatic winding device and wire arrangement of automatic winding device, can solve the problem of uncontrollable number of coils of wire rod, and achieve the effect of eliminating the gap in wedge-shaped area
- Summary
- Abstract
- Description
- Claims
- Application Information
AI Technical Summary
Problems solved by technology
Method used
Image
Examples
Embodiment 1
[0049] Without loss of generality, figure 2 As shown, the present invention provides a method for controlling the wiring of a fully automatic winding device after a deep analysis of the reasons for the technical problem that the number of turns at both ends of the material tray is prone to be uncontrollable during automatic winding. , divided into the following steps:
[0050] S1. Calculate the time t used by the traversing axis of the automatic winding device for each traversing distance L; the unit of t is seconds, and L is the sum of the wire width and the wire gap, and the wire gap is located on the same material tray axis, the same The axial gap between two adjacent coils of wire in the wire layer;
[0051] S2. Split t into t 1 and t 2 , t=t 1 +t 2 ; When the first servo motor receives the commutation pulse signal every time, delay t 1 The length of time to send a pulse signal to the first servo motor, and at t 1 At the end of the time, the duration of sending to ...
Embodiment 2
[0063] In order to further solve the technical problem that the automatic winding device is prone to wedge-shaped gaps at both ends of the tray, Figure 4 As shown, on the basis of Embodiment 1, the present invention further fine-tunes the sum L of the wire width and the wire gap, and by fine-tuning the wire gap of each wire layer, the technical effect that each wire layer is fully wound with wire is achieved. In this technical solution, the data of the number of coils of the wire wound on the same wire layer is very large, and the size of the wedge-shaped gap is evenly dispersed on the wire gap, and the technical principle that the gap after fine-tuning can be ignored visually can achieve the above-mentioned technical effect. . The specific operation is as follows:
[0064] S3. Fine-tuning the L until there is no wedge-shaped area on each layer of the wire layer wound on the reel shaft. The effect is to make the existing wedge-shaped area disappear when winding according to ...
PUM
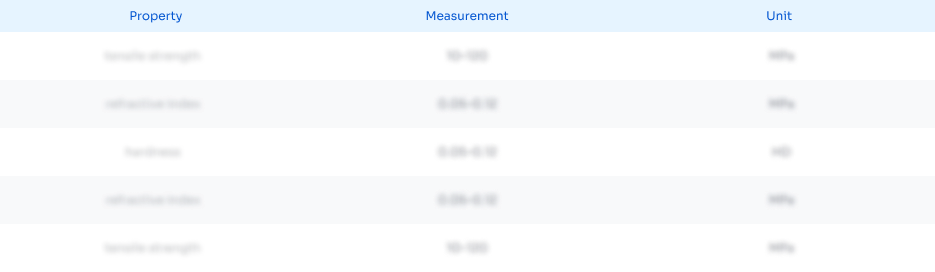
Abstract
Description
Claims
Application Information

- R&D
- Intellectual Property
- Life Sciences
- Materials
- Tech Scout
- Unparalleled Data Quality
- Higher Quality Content
- 60% Fewer Hallucinations
Browse by: Latest US Patents, China's latest patents, Technical Efficacy Thesaurus, Application Domain, Technology Topic, Popular Technical Reports.
© 2025 PatSnap. All rights reserved.Legal|Privacy policy|Modern Slavery Act Transparency Statement|Sitemap|About US| Contact US: help@patsnap.com