A method for estimating hysteretic frictional energy consumption in precision mechanisms with gaps
A precision mechanism, hysteretic friction technology, applied in computing, special data processing applications, instruments, etc., can solve problems such as damage, unsteady vibration, energy consumption effects that cannot be ignored, and achieve improved safety and versatility. Effect
- Summary
- Abstract
- Description
- Claims
- Application Information
AI Technical Summary
Problems solved by technology
Method used
Image
Examples
Embodiment Construction
[0045] The present invention will be described in detail below in conjunction with specific embodiments. The following examples will help those skilled in the art to further understand the present invention, but do not limit the present invention in any form. It should be noted that those skilled in the art can make several modifications and improvements without departing from the concept of the present invention. These all belong to the protection scope of the present invention.
[0046] Such as figure 1As shown, this embodiment provides a method for estimating hysteretic frictional energy consumption in precision mechanisms with gaps. If there is no detailed description in this embodiment, you can refer to the Summary of the Invention. The method includes the following steps:
[0047] 1. Considering that there is inevitably a small gap in the actual kinematic pair, the influence of the hysteretic friction on the surface of the gap cannot be ignored in the precision mechani...
PUM
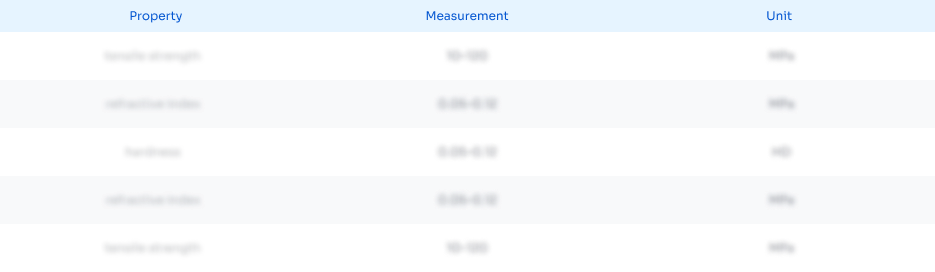
Abstract
Description
Claims
Application Information

- R&D
- Intellectual Property
- Life Sciences
- Materials
- Tech Scout
- Unparalleled Data Quality
- Higher Quality Content
- 60% Fewer Hallucinations
Browse by: Latest US Patents, China's latest patents, Technical Efficacy Thesaurus, Application Domain, Technology Topic, Popular Technical Reports.
© 2025 PatSnap. All rights reserved.Legal|Privacy policy|Modern Slavery Act Transparency Statement|Sitemap|About US| Contact US: help@patsnap.com