A kind of method for preparing hydrazine hydrate
A technology of hydrazine hydrate and benzophenone, which is applied in the direction of hydrazine, nitrogen and non-metallic compounds, etc., can solve the problems of pollution and high purity of hydrazine hydrate, and achieve the effect of simple process, high purity and convenient operation
- Summary
- Abstract
- Description
- Claims
- Application Information
AI Technical Summary
Problems solved by technology
Method used
Examples
Embodiment 1
[0010] Put 130 g of benzophenone into the reactor, add 1.5 g of thorium oxide, 1.5 g of ammonium chloride and 8 g of cuprous chloride respectively, seal the reactor and evacuate it, raise the temperature to 250 ° C, and flow to the reactor at a speed of 0.5 L / min. Ammonia is continuously fed into the reactor, and oxygen is fed into the reactor at a speed of 2L / min at the same time. Under this condition, the reaction is carried out for 8 hours to obtain 65% benzophenone dinitrogen. In the reaction, the oxidation Under the catalysis of thorium and ammonium chloride, benzophenone and ammonia undergo dehydration condensation to generate dibenzylidene amine, and under the catalysis of cuprous chloride, dibenzylidene amine is further oxidatively coupled to form benzophenone diazo, After the reaction, the reaction kettle was naturally cooled to room temperature to separate the benzophenone diazo, and at the same time, the catalyst was centrifuged, washed and recovered for the next rea...
Embodiment 2
[0012] Put 260g of benzophenone into the reaction kettle, add 2g of thorium oxide, 2g of ammonium chloride and 15g of cuprous chloride respectively, seal the reaction kettle and evacuate it, raise the temperature to 250°C, and inject Feed ammonia continuously, and feed oxygen into the reactor at a speed of 2L / min simultaneously, and react under this condition for 10 hours to obtain benzophenone dinitrogen with a content of 65%. In the reaction, thorium oxide and chlorine Under the catalysis of ammonium chloride, benzophenone and ammonia undergo dehydration condensation to generate dibenzylidene amine, and under the catalysis of cuprous chloride, dibenzylidene amine is further oxidatively coupled to generate benzophenone diazo. , the reaction kettle was naturally cooled to room temperature, and the benzophenone diazoxide was separated, and the catalyst was centrifuged at the same time, and recovered after washing for the next reaction. Add 8g of polyethylene oxide and 8g of dod...
Embodiment 3
[0014] Put 650 g of benzophenone into the reaction kettle, add 8 g of thorium oxide, 8 g of ammonium chloride and 30 g of cuprous chloride respectively, seal the reaction kettle and evacuate it, raise the temperature to 250 ° C, and feed the reaction kettle at a speed of 0.5 L / min. Ammonia is continuously passed into the middle, and oxygen is passed into the reactor at a speed of 2L / min at the same time, and the reaction under this condition for 12 hours obtains benzophenone dinitrogen with a content of 60%. In the reaction, thorium oxide and Under the catalysis of ammonium chloride, benzophenone and ammonia undergo dehydration condensation to generate dibenzylidene amine, and under the catalysis of cuprous chloride, dibenzylidene amine is further oxidatively coupled to form benzophenone hydrazine, and the reaction ends Finally, the reaction kettle was naturally cooled to room temperature, and the benzophenone diazoxide was separated, and the catalyst was centrifuged, washed an...
PUM
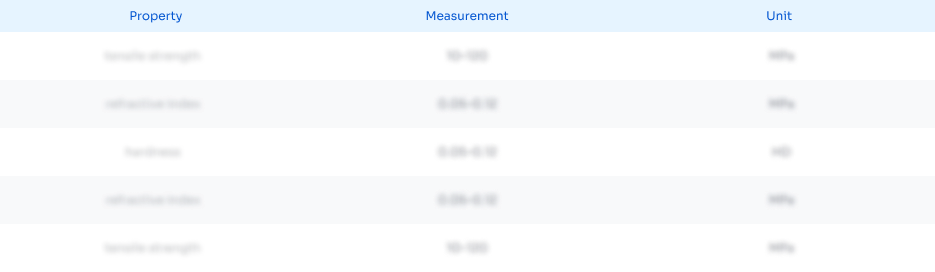
Abstract
Description
Claims
Application Information

- Generate Ideas
- Intellectual Property
- Life Sciences
- Materials
- Tech Scout
- Unparalleled Data Quality
- Higher Quality Content
- 60% Fewer Hallucinations
Browse by: Latest US Patents, China's latest patents, Technical Efficacy Thesaurus, Application Domain, Technology Topic, Popular Technical Reports.
© 2025 PatSnap. All rights reserved.Legal|Privacy policy|Modern Slavery Act Transparency Statement|Sitemap|About US| Contact US: help@patsnap.com