A kind of lamination thermal curing method of wood fiber special-shaped parts
A technology of wood fiber and thermal curing, which is applied in the direction of household components, wood processing appliances, and other household appliances. It can solve the problems of high molding compression ratio, large consumption of log materials, and low production efficiency, so as to increase hardness and internal viscosity. The effect of improving mechanical properties and reducing difficulty
- Summary
- Abstract
- Description
- Claims
- Application Information
AI Technical Summary
Problems solved by technology
Method used
Examples
Embodiment 1
[0014] Embodiment 1: a kind of laminated heat-curing method of wood fiber special-shaped parts, comprising the following steps: A): wood fiber raw materials are sent into the hot air drying pipeline to dry by hot air, the drying temperature is 90 ° C, and after drying, control The water content of the wood fiber raw material is 4%; B): divide the finished furniture piece into two parts, the surface layer and the back layer, the surface layer has the three-dimensional pattern of the furniture piece, and at the same time according to the surface layer and the back layer The target density and target volume of the layer, weigh the quantitative dried surface wood fiber raw material and the back layer wood fiber raw material; C): put the surface wood fiber raw material mass into the corresponding mold for cold pressing, cold pressing The pressure on the wood fiber during the pressing process is 10kg / cm 2 , the press time is 2min, and after the cold pressing is completed, take out t...
Embodiment 2
[0015] Embodiment 2: a kind of laminated heat-curing method of wood fiber special-shaped parts, comprising the following steps: A): wood fiber raw materials are sent into the hot air drying pipeline and dried by hot air, the drying temperature is 160 ° C, and the control is performed after drying. The water content of the wood fiber raw material is 12%; B): The finished furniture piece is divided into three parts: the surface layer and two back layers. The surface layer has the three-dimensional pattern of the furniture piece. Describe the target density and target volume of the back layer, weigh the quantitative dried surface wood fiber raw material and the back layer wood fiber raw material; C): put the surface wood fiber raw material mass into the corresponding mold for cold pressing , the wood fiber bears a pressure of 60kg / cm in the process of cold pressing 2 , the press time is 25min, and after the cold pressing is completed, take out the pressed surface prepress; D): Pu...
Embodiment 3
[0016] Embodiment 3: a kind of laminated heat-curing method of wood fiber shaped parts, comprising the following steps: A): wood fiber raw materials are sent into the hot air drying pipeline and dried by hot air, the drying temperature is 150 ° C, and the drying temperature is controlled after drying. The water content of the wood fiber raw material is 8%; B): The finished furniture piece is divided into four parts: the surface layer and three back layers. The surface layer has the three-dimensional pattern of the furniture piece. Describe the target density and target volume of the back layer, weigh the quantitative dried surface wood fiber raw material and the back layer wood fiber raw material; C): put the surface wood fiber raw material mass into the corresponding mold for cold pressing , the wood fiber bears a pressure of 30kg / cm in the process of cold pressing 2 , the press time is 15min, and after the cold pressing is completed, take out the pressed surface layer prepre...
PUM
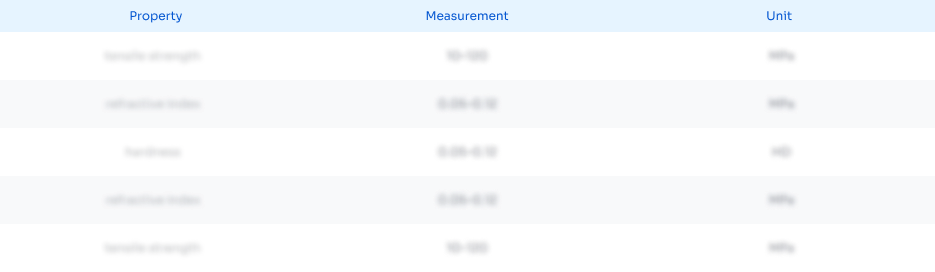
Abstract
Description
Claims
Application Information

- R&D
- Intellectual Property
- Life Sciences
- Materials
- Tech Scout
- Unparalleled Data Quality
- Higher Quality Content
- 60% Fewer Hallucinations
Browse by: Latest US Patents, China's latest patents, Technical Efficacy Thesaurus, Application Domain, Technology Topic, Popular Technical Reports.
© 2025 PatSnap. All rights reserved.Legal|Privacy policy|Modern Slavery Act Transparency Statement|Sitemap|About US| Contact US: help@patsnap.com