Double-faced coating all-in-one machine and coating method thereof
A double-sided coating and integrated machine technology, which is applied to the surface coating liquid device, coating, etc., can solve the problems of inconvenient cleaning, long film running route, and increased number of operators, so as to achieve simple and convenient operation, The effect of reducing labor costs and reducing length dimensions
- Summary
- Abstract
- Description
- Claims
- Application Information
AI Technical Summary
Problems solved by technology
Method used
Image
Examples
Embodiment Construction
[0027] The present invention will be further described below in conjunction with accompanying drawing:
[0028] An all-in-one double-sided coating machine, comprising an organic frame 8, a discharge reel 2 on which a base material 1 is placed, a first coating head 3 for coating the front side of the base material 1, and a first coating head 3 for coating the back side of the base material 1 Two coating heads 4, an oven 5 for drying the substrate 1, a reel 6 for accommodating the substrate, and a plurality of tension control devices that provide tension for the operation of the substrate, the unwinding reel 2, the first coating The cloth head 3, the second coating head 4, the rewinder 6 and the tension control device are all arranged on the frame 8, the rewinder 6 is arranged above the discharge reel 2, and the base material 1 is pulled out from the unwinding reel 2, coated on the front side by the first coating head 3, passed through the oven 5 and then coated on the reverse s...
PUM
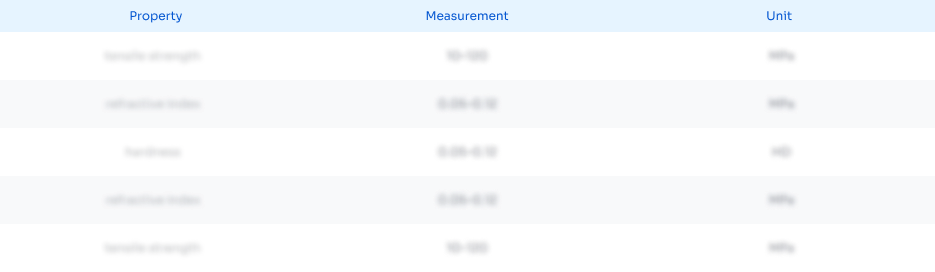
Abstract
Description
Claims
Application Information

- R&D
- Intellectual Property
- Life Sciences
- Materials
- Tech Scout
- Unparalleled Data Quality
- Higher Quality Content
- 60% Fewer Hallucinations
Browse by: Latest US Patents, China's latest patents, Technical Efficacy Thesaurus, Application Domain, Technology Topic, Popular Technical Reports.
© 2025 PatSnap. All rights reserved.Legal|Privacy policy|Modern Slavery Act Transparency Statement|Sitemap|About US| Contact US: help@patsnap.com