Six-foot robot control system and control method thereof
A technology of a hexapod robot and a manipulation system, which is applied to the manipulation system and manipulation field of a hexapod robot, can solve the problems of complex manipulation, poor real-time communication, and poor man-machine coordination and integration.
- Summary
- Abstract
- Description
- Claims
- Application Information
AI Technical Summary
Problems solved by technology
Method used
Image
Examples
specific Embodiment approach 1
[0124] Specific implementation mode one: the operation interface of the hexapod robot manipulation system is as follows: figure 1 Shown; the hexapod robot control system, including the following modules: motor enable control module, stop module, parameter setting module, position reset module, pose control module, gait control module, single-leg control module, standing and retracting control module, wheel control module and position display module;
[0125] The motor enabling control module is used for the power-on control of the robot's action motor;
[0126] The stop module is used for emergency stop and stop control of robot execution actions;
[0127] The display interface of the parameter setting module is as follows: figure 2 As shown; the parameter setting module is to input the parameters of the robot, including:
[0128] LegLength_1 / 2 / 3 parameter input sub-module, that is, base segment length, thigh length and calf length parameter input sub-module; used for base...
specific Embodiment approach 2
[0196] Embodiment 2: The hexapod robot control system is developed on the basis of Visual C++6.0, and communicates with the control system by embedding the dynamic link library Pcomm32 provided by UMAC.
[0197] Other steps and parameters are the same as those in Embodiment 1.
specific Embodiment approach 3
[0198] Specific embodiment three: utilize the method for manipulating a robot with a hexapod robot manipulating system, comprising the following steps:
[0199] Step 1: Run the motor enable control module to make the motor in working state;
[0200] Step 2: Run the position reset module to set the initial position of the robot's legs in the local coordinate system, so that the robot can return to zero;
[0201] Set the initial position of the robot's single leg of the six-legged Choose_CS_1 / 2 / 3 / 4 / 5 / 6 in the local coordinate system, including: the setting of the x position Ed_xPos, the setting of the y position Ed_yPos in the local coordinate system, and the setting of the z position Ed_zPos set up;
[0202] Step 3: According to the actual situation of the robot, run the system parameter setting module and set the system parameters; including:
[0203] Enter LegLength_1 / 2 / 3, that is, the length of the base segment, the length of the thigh and the length of the calf;
[0204]...
PUM
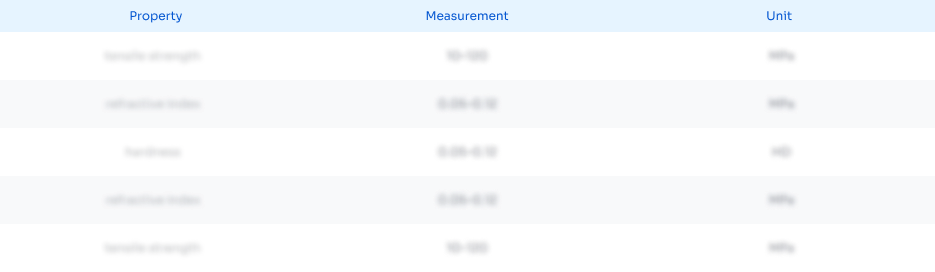
Abstract
Description
Claims
Application Information

- Generate Ideas
- Intellectual Property
- Life Sciences
- Materials
- Tech Scout
- Unparalleled Data Quality
- Higher Quality Content
- 60% Fewer Hallucinations
Browse by: Latest US Patents, China's latest patents, Technical Efficacy Thesaurus, Application Domain, Technology Topic, Popular Technical Reports.
© 2025 PatSnap. All rights reserved.Legal|Privacy policy|Modern Slavery Act Transparency Statement|Sitemap|About US| Contact US: help@patsnap.com