Rubber-sealed sensor and its manufacturing process
A manufacturing process and sensor technology, which is applied in the field of rubber-sealed sensors and its manufacturing process, can solve problems such as difficult to meet assembly accuracy, long sensor requirements, and large sensor size errors, so as to prevent the sensor head from bulging or cracking, and assembly Simple process and good sealing effect
- Summary
- Abstract
- Description
- Claims
- Application Information
AI Technical Summary
Problems solved by technology
Method used
Image
Examples
Embodiment Construction
[0065] The present invention will be further described in detail below in conjunction with the accompanying drawings and specific embodiments.
[0066] The glue-sealed sensor provided by the present invention can be used for active sensors and passive sensors, and is especially suitable for active sensors, such as Figure 7 As shown, it includes a bracket 1 , a Hall chip 2 , a circuit board 3 and an O-ring 4 .
[0067] Such as figure 2 As shown, the Hall chip 2 has a sensor element 21 and a chip PIN needle group 22, the sensor element 21 is located at the head of the Hall chip 2, and the Hall chip 2 is integrated with a magnet on the rear side of the sensor element 21, and the chip PIN The fixed end of the pin group 22 is close to the sensing element 21 , and the free end is bent towards the tail of the chip with a certain gap between it and the top surface 23 of the chip.
[0068] The circuit board 3 is a hard circuit board, including a substrate 31, a circuit board PIN pi...
PUM
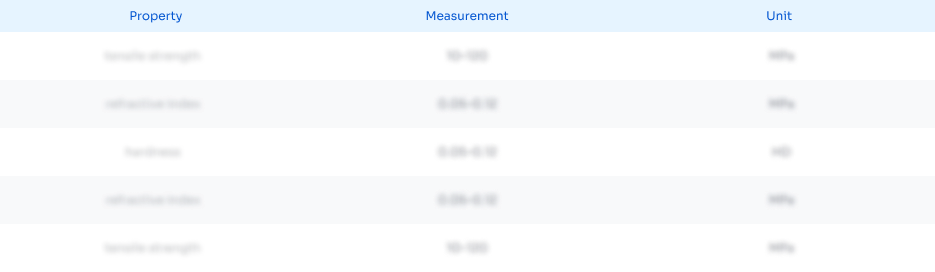
Abstract
Description
Claims
Application Information

- R&D Engineer
- R&D Manager
- IP Professional
- Industry Leading Data Capabilities
- Powerful AI technology
- Patent DNA Extraction
Browse by: Latest US Patents, China's latest patents, Technical Efficacy Thesaurus, Application Domain, Technology Topic.
© 2024 PatSnap. All rights reserved.Legal|Privacy policy|Modern Slavery Act Transparency Statement|Sitemap