Flexible bionic tail fin with embedded drive joints and multiple motion modes
A multi-motion mode, intra-joint technology, applied to non-rotating propulsion elements and other directions, can solve the problems of high maintenance and replacement costs, complex structure, single motion mode, etc., and achieve the effect of high motion execution efficiency and easy installation.
- Summary
- Abstract
- Description
- Claims
- Application Information
AI Technical Summary
Problems solved by technology
Method used
Image
Examples
specific Embodiment approach 1
[0015] Specific implementation mode one: combine Figure 1-Figure 5 Explain that the flexible multi-motion mode bionic caudal fin with built-in driving joints in this embodiment includes a bionic flexible skin 5, an elastic clamping frame 1, a first piezoelectric fiber composite driving joint 4 and N second piezoelectric fiber composite Material-driven joint 3; where N is an even number, and N≥2;
[0016] The elastic clamping frame 1, the first piezoelectric fiber composite material driving joint 4 and N second piezoelectric fiber composite material driving joints 3 are embedded in the flexible skin 5, the first piezoelectric fiber composite material driving joint 4 and the Nth Two piezoelectric fiber composite driving joints 3 are detachably connected to the elastic clamping frame 1 respectively. The first piezoelectric fiber composite driving joint 4 is horizontally arranged in the middle of the bionic flexible skin 5 along the axial direction. N second piezoelectric The fi...
specific Embodiment approach 2
[0018] Specific implementation mode two: combination Figure 1-Figure 3 Note that the bionic flexible skin 5 in this embodiment is made of silica gel. With such setting, the chemical properties are stable, and the mechanical strength is relatively high, which meets the design requirements and actual needs.
specific Embodiment approach 3
[0019] Specific implementation mode three: combination Figure 1-Figure 3Note that the elastic clamping frame 1 in this embodiment is made of silica gel or polytetrafluoroethylene. With such a setting, it is convenient to use and easy to obtain materials. Others are the same as in the first or second embodiment.
PUM
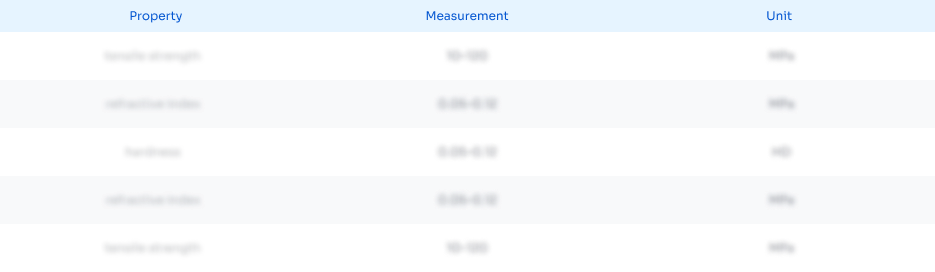
Abstract
Description
Claims
Application Information

- R&D
- Intellectual Property
- Life Sciences
- Materials
- Tech Scout
- Unparalleled Data Quality
- Higher Quality Content
- 60% Fewer Hallucinations
Browse by: Latest US Patents, China's latest patents, Technical Efficacy Thesaurus, Application Domain, Technology Topic, Popular Technical Reports.
© 2025 PatSnap. All rights reserved.Legal|Privacy policy|Modern Slavery Act Transparency Statement|Sitemap|About US| Contact US: help@patsnap.com