Co-location device for automatically butting and assembling large-sized thin-wall barrel-shaped members
A technology of co-location and automatic docking, applied in the field of devices in the field of assembly and docking technology, can solve the problems of not meeting the requirements of modern production, high initial positioning requirements of parts to be assembled, distortion and deformation of thin-walled parts, etc., so as to improve docking efficiency and docking. Accuracy, solving the effect of uneven quality of components and small flexible deformation
- Summary
- Abstract
- Description
- Claims
- Application Information
AI Technical Summary
Problems solved by technology
Method used
Image
Examples
Embodiment 1
[0036] Such as figure 1 As shown, in this embodiment, two sets of positioning mechanisms 2 that are movable on the track 1 and have a C-shaped bracket 3 are fixedly connected with the component 4 to be adjusted.
[0037] Such as Figure 4 As shown in -6, the positioning mechanism 2 includes: a sliding chassis 5, a lateral attitude adjustment platform 6, a vertical attitude adjustment platform 7 and a rotating attitude adjustment platform 8, wherein: the sliding chassis 10 with a screw mechanism 12 has x In the attitude adjustment function, the lower part of the horizontal attitude adjustment platform 6 is connected to the x-direction moving pair through the guide rail slider 11 and the sliding chassis guide rail 18, which is driven by the screw mechanism 12; The platform 6 rails are connected to form a y-movable pair, which is driven by a screw mechanism 12;
[0038] A sliding wheel set 9 is provided below the sliding chassis 5, and the sliding wheel set 9 is in rolling cont...
Embodiment 2
[0050] Such as figure 2 As shown, this embodiment is realized by three sets of positioning mechanisms 2. The coordinated positioning device composed of the three sets of positioning mechanisms has at least six active driving combinations, and the driving form is 2‐2‐2 arrangement (the first positioning mechanism yz active drive, the second positioning mechanism xz is actively driven, and the third positioning mechanism yz is actively driven); in addition, one of the three C-shaped brackets 3 needs to have an active drive.
[0051] In this embodiment, the overall layout of the tooling is as follows figure 2 As shown, the positioning mechanism such as Figure 4 As shown in -6, the screw mechanism driven by the motor has the function of adjusting the attitude in this direction. The positioning mechanisms along the x-axis direction are the first positioning mechanism, the second positioning mechanism, and the third positioning mechanism. The structure diagram of the C-shaped br...
Embodiment 3
[0059] Such as image 3 As shown, the present embodiment adopts four sets of positioning mechanisms 2 to realize. The cooperative positioning device composed of the four sets of positioning mechanisms has at least seven active driving combinations, and the driving form is 2-2-1-2 arrangement (the first positioning mechanism yz is actively driven, the second positioning mechanism xz is actively driven, the third positioning mechanism z is actively driven, and the fourth positioning mechanism yz is actively driven); in addition, one of the four C-shaped brackets 3 needs to have an active drive.
[0060] In this embodiment, the overall layout of the tooling is as follows image 3 As shown, the positioning mechanism such as Figure 4 As shown in -6, the screw mechanism driven by the motor has the function of adjusting the attitude in this direction. The positioning mechanisms along the x-axis direction are the first positioning mechanism, the second positioning mechanism, the thi...
PUM
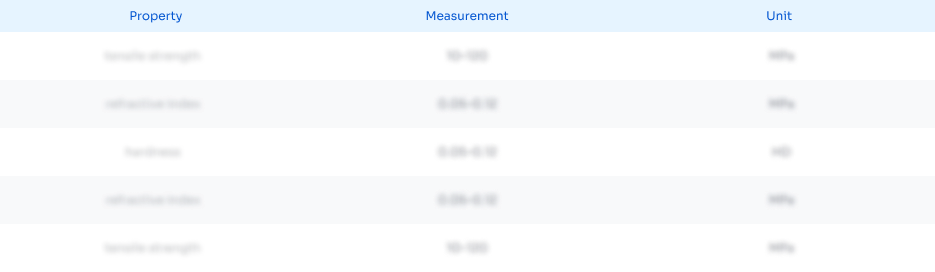
Abstract
Description
Claims
Application Information

- R&D
- Intellectual Property
- Life Sciences
- Materials
- Tech Scout
- Unparalleled Data Quality
- Higher Quality Content
- 60% Fewer Hallucinations
Browse by: Latest US Patents, China's latest patents, Technical Efficacy Thesaurus, Application Domain, Technology Topic, Popular Technical Reports.
© 2025 PatSnap. All rights reserved.Legal|Privacy policy|Modern Slavery Act Transparency Statement|Sitemap|About US| Contact US: help@patsnap.com