A piezoelectric sensor pretensioning device
A technology of piezoelectric sensors and force bearing blocks, which is applied in the application field of piezoelectric quartz sensors in the field of three-dimensional force measurement, and can solve the problems of limiting the precision and accuracy of piezoelectric force measurement structures, single preload direction, and force measurement structures. Complicated and other issues, to achieve the effect of simple structure, easy adjustment, and enlarged measurement area
- Summary
- Abstract
- Description
- Claims
- Application Information
AI Technical Summary
Problems solved by technology
Method used
Image
Examples
Embodiment Construction
[0010] The specific implementation of the present invention will be described in detail below in conjunction with the accompanying drawings and technical solutions.
[0011] In the existing method of applying preload to the piezoelectric quartz sensor, since the preload always has a certain rigidity of the elastic body and is connected in parallel with the rigidity of the sensor, a load sharing effect will inevitably occur, that is, the measured external force cannot be 100% The ground is transmitted to the sensor, which affects the accuracy of the measurement. This embodiment adopts as figure 1 , 2 In the shown structure, the upper and lower three-directional piezoelectric sensors 2, 8 all have a central hole. During installation, first screw the lower part of the stud 3 into the threaded hole d of the lower press block 6, and then install the lower three-way force sensor 8 so that the stud 3 passes through the center hole of the lower three-way force sensor 8 , ensure tha...
PUM
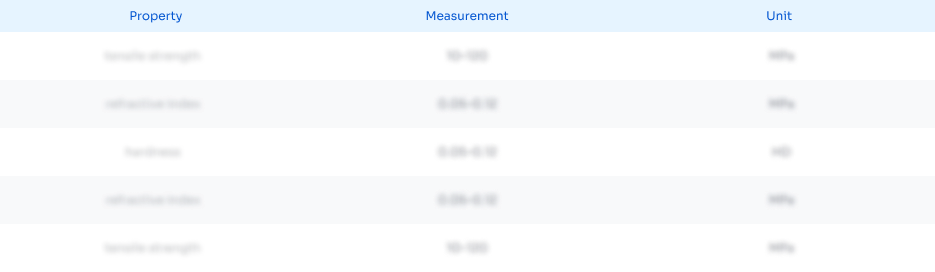
Abstract
Description
Claims
Application Information

- R&D
- Intellectual Property
- Life Sciences
- Materials
- Tech Scout
- Unparalleled Data Quality
- Higher Quality Content
- 60% Fewer Hallucinations
Browse by: Latest US Patents, China's latest patents, Technical Efficacy Thesaurus, Application Domain, Technology Topic, Popular Technical Reports.
© 2025 PatSnap. All rights reserved.Legal|Privacy policy|Modern Slavery Act Transparency Statement|Sitemap|About US| Contact US: help@patsnap.com