Digital Manufacturing System For Printing Three-Dimensional Objects On A Rotating Surface
A printing head and inner surface technology, which is applied in processing and manufacturing, manufacturing tools, additive manufacturing, etc., can solve the problems of 3D printer speed limit and other issues
- Summary
- Abstract
- Description
- Claims
- Application Information
AI Technical Summary
Problems solved by technology
Method used
Image
Examples
Embodiment Construction
[0014] figure 1 and figure 2 A printer 100 for generating a three-dimensional object 20 is shown. The printer 100 includes an outer frame 22 configured to support a rotatable hollow member 24 and an inner frame 26 configured to hold a first printhead 28 ( figure 2 ) is supported in the hollow part 24. The outer frame 22 is also configured such that the hollow member 24 can rotate about an axis 30 relative to the inner frame 26 . The hollow part 24 has at least one wall 32 forming a continuous inner surface 34 or base material around the axis 30 . Rotation of hollow part 24 about axis 30 (in the direction of arrow 36) causes a portion of inner surface 34 of wall 32 to be along machine direction 38 ( figure 2 ) moves past the first print head 28. The arrangement of the first printhead 28 within the hollow member 24 enables the first printhead 28 to eject material onto the inner surface 34 of the wall 32 in a direction generally away from the axis 30 . As used herein, th...
PUM
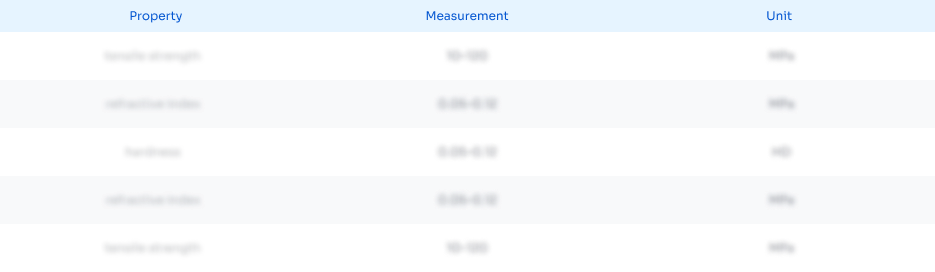
Abstract
Description
Claims
Application Information

- R&D
- Intellectual Property
- Life Sciences
- Materials
- Tech Scout
- Unparalleled Data Quality
- Higher Quality Content
- 60% Fewer Hallucinations
Browse by: Latest US Patents, China's latest patents, Technical Efficacy Thesaurus, Application Domain, Technology Topic, Popular Technical Reports.
© 2025 PatSnap. All rights reserved.Legal|Privacy policy|Modern Slavery Act Transparency Statement|Sitemap|About US| Contact US: help@patsnap.com